by Dianna Brodine, managing editor, Plastics Business
Solving the talent problem in the US manufacturing industry has been – and will continue to be – a priority for plastics processors. Perhaps traditionally seen as a job for men, women increasingly are stepping up to take roles in manufacturing facilities. Four women at the top of the profession spoke with Plastics Business to discuss their start in the industry (three of the four succeeded in a family business), the role a strong mentor can play in encouraging success and the steps that manufacturers can take to encourage more women to look at jobs in the industry.
Getting their start
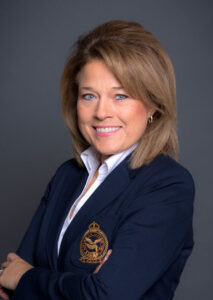
Behrendt: My parents founded the company in 1983 when I was in middle school, starting with two machines and two employees in a 3,000 sq. foot building. This grew to 145,000 sq. ft. in Webster City, Iowa, and 40,000 sq. ft. in Falls City, Nebraska, with 49 presses. When I was younger, I didn’t have the intention of coming back to the family company. I wanted to work within pharmaceutical sales, so I found a way in – and then realized I didn’t like being a road warrior all the time. Coming back to work for your parents is a big change after being self-managed, but the manufacturing industry wasn’t a hard choice for me because I grew up in this company. As my parents grew the business, I would help with answering phones, cleaning, running machines or delivering what I could once I could drive. When I came back to the business, I was able to step into the sales growth and networking that have always been my passion with roles in sales and marketing, and then purchasing. Near the end of 2008, I began my role as CEO and became an owner of the company with my sister and parents. The company was sold on September 18, 2020, to Angstrom Automotive Group.
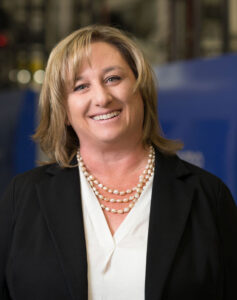
Barras: I grew up in the industry. My parents started Westec in 1969, but I never thought I’d wind up working in plastics – I was studying Psychology in college. But, after moving back to California from Virginia, I needed a job…and Westec had an opening in customer service. For 27 years, I’ve worked in several different departments – customer service, accounting, payroll and program management. It’s been a little odd – my second shift foreman has been here for 39 years, so he’s known me since I was 11. We have a lot of family history here, but that also means I had to prove myself to everyone – my dad, other employees and those outside the company. In all of my roles with the company, I never reported to my parents until 2012. Then in 2013, I was promoted to director of customer relations, and then to vice president in 2015 before taking over as president in January 2016.
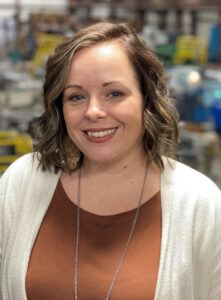
Enochs: My grandfather started the company in 1979, and my grandmother was a senior leader, so I was raised in manufacturing and in the plastics industry. Seeing my grandmother in a leadership role made me want to be in that leadership role as well, and I spent a lot of time sitting behind her desk pretending to be the boss. I began in a professional capacity right out of high school, working mainly in our accounting department, and then I majored in business administration and management in college so I could focus on the operations side of the business. But where I really started to get a grasp on where we were going to grow and change was in human resources. I was given the opportunity for an HR management role in 2008 at the height of the recession. I was thrown into a whirlwind of what it means to be compassionate and how you handle people in times of distress. That also was just a couple of years after my grandfather had passed away. Losing him and then going through organizational struggles during the economic downturn solidified my desire to be the next leader of the organization. I was 27 at the time. I went to my grandmother late in 2018 and told her I was ready, and I was formally promoted to the CEO position last July.
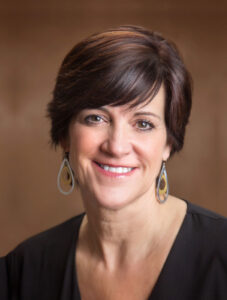
Walker: My career in manufacturing was not planned, but my career in leading people was. My degree in Industrial and Labor Relations from Cornell University solidified for me the great desire I had to have a positive impact on employee lives every day. Upon graduation, I worked for Mobil Oil and Chemical in the company’s upstate New York operations. I then accepted an employee relations role with Schlegel Corporation, a company that had just started a venture (TASUS) for our current parent company, Tsuchiya Co. Ltd of Nagoya Japan. I seized upon the opportunity to move to Bloomington, Indiana, and assume the role of human resources and finance manager to help start this new venture. I became the president of TASUS a couple of years later. It was a lot by chance and not by design. I’ve always told my kids to just get out there and work, because that gives you your answers about what you want to do in your career. I learned that I thrived better in an environment where I could wear a lot of hats, which is typical in a mid-sized company. I am, oddly enough, the CEO of a plastics injection molding company with no engineering background or prior manufacturing experience. It’s been all about leading people, having a vision and recognizing that if we have the right employee culture, the bottom line can take care of itself.
Leading women in the industry
Behrendt: Vantec Inc. was certified Woman Owned by WBENC up until we became a part of the Angstrom Automotive Group. Now, we can be certified as a minority-owned business so that our customers still can enjoy the diversity metrics that they were benefitting from previously. We roughly have 50% women at Vantec LLC throughout production and leadership, out of 190 employees. I wouldn’t say it was a choice, that’s how it happened. Clearly, I don’t believe we should treat anyone differently, no matter who they are – hiring is based on who is best for the job. But even when I look back at the picture of Vantec from 1994 when we were ISO-certified, we had a number of women in that picture.
Barras: Of our 95 employees, 66 of us are female! Our upper management team consists of 10 members, four of which are female, including our controller, purchasing manager, quality assurance manager and me. The majority of our machine operators also are female, and a good portion of us in the office are female. It’s not intentional. I just need somebody who can do the job, and I would guess that the majority of the people who are hired don’t even know when they’re interviewed that the company is run by a female. We do have several families who work here at Westec – for instance, we have four sisters on first shift, and they’ve been here almost 20 years. And, we do offer referral incentives, so that could be part of it. We take care of our employees.
Enochs: Currently we have about 35 women employed across the organization, from entry level positions all the way to CEO, with a total of 70 employees. For us, diversity and inclusion has always been a core value so, while we don’t specifically seek out women for roles in any capacity in the organization, our hiring practices always have included making sure we have representation from all capacities, whether women, men or minorities. We started as a minority business – my grandfather was native Western Cherokee.
Walker: Our plants are about 40% women. The headquarters, which I thought was interesting, is at 39%. As I looked at it, I realized our headquarters is heavily influenced by the engineers who design and build our automation and tooling. That skews the numbers, because we all know there aren’t a lot of female engineers out there. At the plants, we’ve always looked for women in leadership roles. I’ve had female plant leaders and often have female HR managers, quality managers and program managers.
Mentors make a difference
Behrendt: I was mentored by a number of people in my life, but my father had the biggest influence on me. He was running North American operations for a company that was the largest construction company in the world at the time. I saw him work hard, traveling all over in commercial and corporate jets, and thought, “Wow, this is what I want to do.” My parents started Vantec after he left his role at Blount. Mary Andringa, chairman of the board of Vermeer Corporation, also has filled that mentor role. She recruited me to the National Association of Manufacturing (NAM) board. She was the first female to ever chair NAM, which I thought was cool, and now I’m the first female chair of the Manufacturing Excellence Network within the Young Presidents Organization (YPO), where I had many mentors within manufacturing. I feel like I’m following Mary’s lead in that.
Barras: I can’t say that I’ve ever had anyone specifically mentor me. Obviously, I’ve watched, listened and learned from my parents throughout the years, and I’ve taken several classes and seminars on leadership, which all have helped me grow into the person I’ve become. We also have a management consultant who works with our team using the Myers Briggs personality test, and this has been a huge learning tool for me to understand how others process their thoughts and how best to manage or work with each personality type. This question was interesting for me – as a woman, I think we sometimes tend to put ourselves last. We tend to find solutions for others before finding support for ourselves! But I’ve been blessed to be surrounded by a really strong team, and we all mentor each other. We’ve grown together. We’ve taken the business and tripled our sales in the last eight years and it’s amazing to look at the team I have and say, “We did that.”
Enochs: John Keighly has been my formal mentor, a local business owner who owned multiple plastics molding companies. From the first time we met, he reminded me a lot of my grandfather, so there was an ease to our conversations, but he only accepted a mentorship role contingent on the fact that the organization remained a legacy company. He did not want to mentor me into selling the organization. He’s been an excellent tool in my tool pouch, especially as I was going into a new position and a new part of my career. I also have an informal mentor – a woman I’ve looked up to for many years named Shelly Heller. We are very parallel in our experiences – she grew up in her father’s business and when her father stepped back from the organization, I got to watch the transformation not only in her business but also in her. She’s also been an integral part of our company gaining our WBE certification.
Walker: When I was at Cornell as a full-time student working full time, I interviewed for an open position with the associate dean of the college. She wouldn’t hire me because it was just enough money that she was afraid I wouldn’t move on. Even though it didn’t seem helpful at that moment, she became the person I went to for advice and was amazing at helping me make decisions about moving through my education and on to my career. Once I got to Indiana, I was somewhat on my own. While community leaders and others influenced me, the one organization that really helped the most was the Young Presidents Organization. I was in a small group with really bright people who had lived a lot of life and run some good companies, so they were instrumental in my development and maturation in my role and in manufacturing. I can’t really recall my parents or anyone encouraging me to find a mentor or reach out to someone to get advice, but I have found younger women to be more inclined to look for that than we might have been. Maybe it’s just something we’ve learned is valuable, and we can encourage young people to take advantage of it.
Can women be the answer to the talent problem in manufacturing?
Behrendt: Anyone can do whatever they set their mind to, if they want it bad enough – that was almost a quote from my parents when I was growing up. Maybe it’s because they only had girls – I’m the youngest of two, and we both worked at the plant. Now, it’s up to us to get young women interested and involved. STEM in K-12 schools is very important in that effort. There were too many years of schools encouraging every student to go to college, but not everyone has to come out of college with debt. Instead, students can go into the trades and learn skills within the industries. Schools, parents and teachers have to let young women know they’re capable of anything – they can become good in technology and take on STEM roles. We’ve hosted Manufacturing Day tours a number of times, bringing in young students to let them play with the plastic and see the robots. Manufacturing isn’t just one type of job – you can build tools or program robots. It takes all types of people and skill sets.
Barras: Absolutely, woman can be the answer. Women are just as capable as men in the manufacturing world, but we need to present these options to them when they’re young and still in school. STEM and the FIRST Robotics competition are amazing ways to introduce young girls to the possibilities of the manufacturing world. My nine-year-old niece asked for a 3D printer for Christmas! Her school offers design classes using CAD, and she already is learning to design. My brother is a high school teacher in New Jersey, and he coaches the school’s robotics team for the annual FIRST Robotics competition. This presents an amazing team model for kids to work together to plan, design, create and build a robot using CAD, CNCs and other equipment. On his team, the lead engineers have been mostly female for the last three years. We also work with San Jose State University and do a minimum of two shop tours a year for a design manufacturing class. It makes a difference when they see the manufacturing environment, rather than just hear about it. This was totally lost on our generation. We were supposed to grow up and be teachers and office workers. My school didn’t offer wood shop, and we certainly didn’t have classes that would promote students wanting to get into tool design or learning CAD. Today, I see it spinning back a little bit and that’s a good thing as those in skilled positions retire, and we have to be able to fill their positions.
Enochs: It’s important that we promote our manufacturing businesses and open positions in more women-centered areas. For example, we’ve got WBENC, and we make sure to engage with WBENC to promote our job opportunities through those channels. For me, being on LinkedIn and making sure I’m connecting with other women like me is important. Then, when I post a job opportunity, I can reach other women in related fields, which tends to get the word out even faster. Women have big networks, and. I use that network to promote my business and available job openings so we can get more women engaged in manufacturing. I also have two colleagues that I work with who have started nonprofits that pertain specifically to young women in STEM-related fields. These organizations are geared toward young women in urban locations who may not have access to mentors or STEM educational opportunities. The key is getting them early – making sure they’re not already halfway through their high school careers. We need to expose them to the STEM-related fields when they’re in junior high. In some ways, I think girls are afraid to compete against the boys – even now, in 2020 – which is ridiculous. A strong role model can show them what’s possible.
Walker: I have spent my career talking to girls in middle school and high school about my career and how girls could get to where I am. We have to start by letting girls know it’s an option – and it’s a good option – because women can have a very good career in manufacturing. I talk to them a lot about robotics and automation, the joy of making something and the varied type of employees. It’s important to give them this big, round picture of what manufacturing looks like. And, we have made some headway in educating guidance counselors, because manufacturing often isn’t on a list of career choices they talk to their students about. We’ve spent time bringing teachers and guidance counselors in for a full day of education or an afternoon of plant tours, and that has an impact. Students and teachers alike often are surprised when they walk through a spotless plant filled with cool technology and new equipment. They’re wowed by it. That is something we can and need to do regularly. By the time students are in college, they often have a path set before them. The middle school and high school levels are where we’ve got to get them, and it’s our responsibility to develop their interest.