by Brittany Willes, contributing writer, Plastics Business
Well aware of the growing concerns surrounding plastic recyclability and sustainability, Plastikos, Inc., located in Erie, Pennsylvania, has taken steps to be at the forefront in addressing these issues. The custom injection molder and its sister company Micro Mold believe “success isn’t simply measured in dollars and cents. It’s the satisfaction of knowing that we help our customers deliver revolutionary products – and that their end users benefit greatly from our involvement,” according to the company’s website. The company cites environmental stewardship as one of its pillars.
In late 2019, injection molder Plastikos, Inc., launched Plastikos Medical – a division of the company that focuses on manufacturing precision molded products for Class II and Class III medical devices. Along with producing high-quality products, one of the biggest goals for Plastikos Medical was to ensure that the parts being produced were done so at the highest level of sustainability. According to Dan Snyder, technical sales manager, Plastikos has a history of tailoring processes to account for good sustainability and stewardship practices.
“We’ve always had a focus on environmental stewardship,” said Snyder, “especially from a leadership aspect. Minimizing our environmental footprint has been a key component to how our businesses operate.”
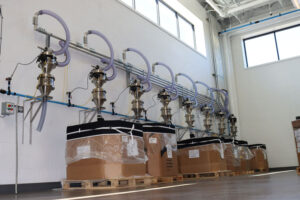
As such, leadership set itself a rigorous standard for developing a method of reusing or recycling 100% of waste generated from the runner systems used to produce its customers’ products. Considering the production of many single-use medical devices often results in high amounts of waste, the emphasis on reuse and/or recycle of materials becomes even more important.
The first step in cutting down on unnecessary waste comes from working directly with customers. Plastikos Medical places significant emphasis on working hand-in-hand with its clients at the very start of any project to design and produce products with an aim toward reducing raw material consumption – typically via full hot runner systems. However, utilizing a hot runner system is not applicable for all projects. In these cases, the result is often a much higher amount of material consumption and regrind.
To address the regrind material not used for the finished product, Plastikos has partnered with a variety of recycling partners. In fact, by mid-2020, Plastikos already had generated approximately 60,000 pounds of regrind, all of which was either reused or recycled.
“There are certain Class I applications (meaning they have no contact with patients) where reground resins are permitted,” explained Snyder. “For our business though, regrind is generally not permissible.” Plastikos’ partners are able to take the company’s high-quality regrind and repurpose it for other non-medical applications where regrind is permitted. “Working with other resin recyclers has been key to avoiding unused material from entering the landfill.”
As Snyder mentioned, “Our goal was to recycle 100% of the material that we could not use in the molded product.” Thanks to its various efforts with its recycling partners, as well as an emphasis on automation to minimize material handling and direct labor, Plastikos has not only met its goal but surpassed it. “Now our goal is to reduce unused resin by continuing to work with clients up front to implement full runner-less systems, where applicable.”
Part of the company’s efforts to further reduce material consumption includes retooling and retrofitting molds. “Right now, we have a major effort in place to retrofit several older high-running tools with hot runner systems,” stated Snyder. As hot runner technologies continue to improve and advance, it is not only Plastikos that benefits from the evolving technology. Clients also are benefiting from the company’s commitment to generating less waste and greater recycling. For instance, new side-gated hot runner systems are proving to offer considerable cost savings for clients.
With the newer hot runner systems, “We can typically attain faster cycle times, which benefits our clients in terms of cost savings,” said Snyder. Plus, “There is essentially no wasted material as a result of the runner system.” Good news for those looking to enhance their environmental sustainability.
Of course, there are some drawbacks with any new technology. “The downside, of course, is the cost of the hot manifold and controller,” said Snyder. “You need to have the volumes on the device to justify the upfront capital.” For many clients, the upfront costs are becoming less of a concern.
Given its commitment to reduced material consumption and greater resin reuse/recycling, it should come as little surprise that these are not the only efforts Plastikos Medical has taken as it strives to maintain high standards of environmental stewardship. When the Plastikos Medical facility was designed, it was with an eye toward maximizing natural lighting throughout. From the Cleanroom Molding Floor to the warehouse to the loading docks, natural lighting has been used where possible to cut down on the amount of electricity used. Additionally, the company installed highly efficient LED lighting where natural lighting was not sufficient. Other measures include a stormwater management collection system, reduced CO2 output and more.
As climate change continues to be a hot button issue, consumers are demanding more transparency and greater sustainability from the products they consume. Everything from drinking straws to medical devices had become subject to intense scrutiny. As such, companies like Plastikos Medical are leading the way in reimagining the design and production process of vital plastics products and will continue to invest in environmentally friendly processes that benefit both company and customer.