Process Simulation
A look at process simulation in plastics manufacturing using computer modeling to virtually test, experiment and/or train to validate the methods and procedures for optimal conditions of the processes. Through simulations, including production, inventory, assembly and transportation, companies may optimize results while reducing time and costs during actual outputs.
INCOE Corporation
248.616.0220
www.incoe.com
INCOE Corporation, Auburn Hills, Michigan, is a complete hot runner solution provider for injection molded applications. Begins with technical advising that includes mold filling simulation (Fig.1) with analysis and when including Opti-Flo® melt management technology includes Finite Element Thermal analysis (Fig.2). These services are provided by INCOE’s technical team and included with the purchase of an INCOE hot runner system. Filling simulations that require a certified “Expert” level also are available.
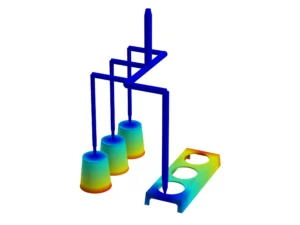
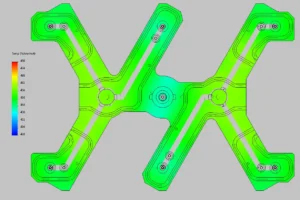
Kruse Training
239.351.7428
www.krusetraining.com
In an industry where precision, speed, and innovation are paramount, the mold design and manufacturing sector constantly seeks solutions to bridge the skills gap and empower a new generation of engineers. Kruse Training, Naples, Florida, a pioneer in cutting-edge educational methodologies, is making significant strides in this direction by launching its Molding Expert injection molding virtual reality (VR) application. This application is a cornerstone of Kruse Training’s eLearning platform, designed to recruit and develop a highly skilled engineering workforce through immersive virtual reality training methods.
SIGMASOFT® Virtual Molding
847.558.5600
www.sigmasoftvm.com
SIGMASOFT® Virtual Molding is a full-process simulation software that helps you overcome the challenges associated in the development, mold design, and production in injection molding. SIGMASOFT® uses a modern, intuitive graphical user interface and integrates multiple process-specific models and 3D-simulation technologies which are developed, validated and continuously optimized, also in the metal casting product, for more than 30 years. This enhanced simulation approach is of outstanding added value compared to conventional simulation approaches available for injection molding. Successful injection simulation always considers ALL the objectives and variables of our customer’s real-life requirements. We can consider all of your requirements in one optimization. n