By Liz Stevens, writer, Plastics Business
The US manufacturing industry continues to face challenges recruiting workers. Colleges and universities are helping to address the problem by offering plastics-oriented courses and credentials, ranging from degree programs that equip young adults with an educational foundation in the industry to credential programs designed for working professionals. What are colleges offering, and what might they need from industry partners to support manufacturing in a way that will fill its needs?
In doing research for this article, more than 1,100 colleges, universities and technical schools were found that offered education related to what happens on a plastics molding plant floor, including certificates and degrees related to composite materials, manufacturing engineering, industrial maintenance technology and injection mold setup. But, if most readers were asked to provide a list of colleges offering education related to plastics, they probably could come up with five or six.
Plastics Business surveyed institutions on the West Coast, East Coast, in the Great Lakes area and in the central Midwest to get insight into a range of plastics-oriented educational offerings. Some of these programs are what those in the industry would consider the ‘cornerstones’ of plastics education, and others are smaller entities doing important work in their region. With institutions in every state working to train students in all aspects of plastics processing, young adults and established professionals are preparing for careers in the industry. Employers just need to know where to look.
Cal Poly Pomona
California State Polytechnic University-Pomona, www.cpp.edu, is a four-year public institution located in Pomona, California. Vishu H. Shah, an instructor and SPE member, answered questions about the university’s College of Professional and Global Education (CPGE) program, which offers a certificate program to current employees of various industries. In operation since 2003, more than 1,200 plastic professionals have gone through the program; enrollment is about 40 students each year.
According to the university’s website: “This three-course certificate program provides practical instruction applicable to materials, processing, product design and tooling. The main emphasis is on practical aspects of Plastics Engineering Technology without being extremely technical so that the knowledge achieved can be applied in day-to-day applications.”
Which industry professionals make up the majority of enrollment for the certificate program?
For the Plastics Theory and Practice course, the audience is non-technical, sales and marketing, newcomers to the plastics field, quality assurance, buyers, innovators and anyone seeking general knowledge about the plastics industry. For the Product Design and Tooling course, the audience is product designers, toolmakers and engineers. And for the Scientific Injection Molding class, we see molding personnel, tool makers, engineers and operation managers.
How is Cal Poly partnering with the manufacturing community in your area?
We are in touch with local molders, toolmakers and plastics material suppliers through email, LinkedIn and our CPGE website. Last year, we partnered with a company in Carlsbad to provide hands-on learning.
What types of manufacturing businesses in your community make good partners?
Plastics processors, tool makers, and material and equipment suppliers. One local molding machine supplier sends its employees and recommends us to customers. Our program began 20 years ago; many plastics professionals are aware of it.
In support of promoting your certificate program, what added visibility would be most helpful?
Exposure beyond Southern California since the in-person program also is offered synchronous online. Personal contact and email campaigns to HR personnel would be helpful; many have a training and education budget.
Do you use social media platforms for promoting the program? What kind of response have you seen?
CPGE’s marketing team replied: “We promote the program through Instagram, Facebook and LinkedIn. The posts get a good number of impressions and a fair number of clicks. We also send e-blasts to our mailing list for that program. People can join the list by filling out a form on our website.”
Ferris State
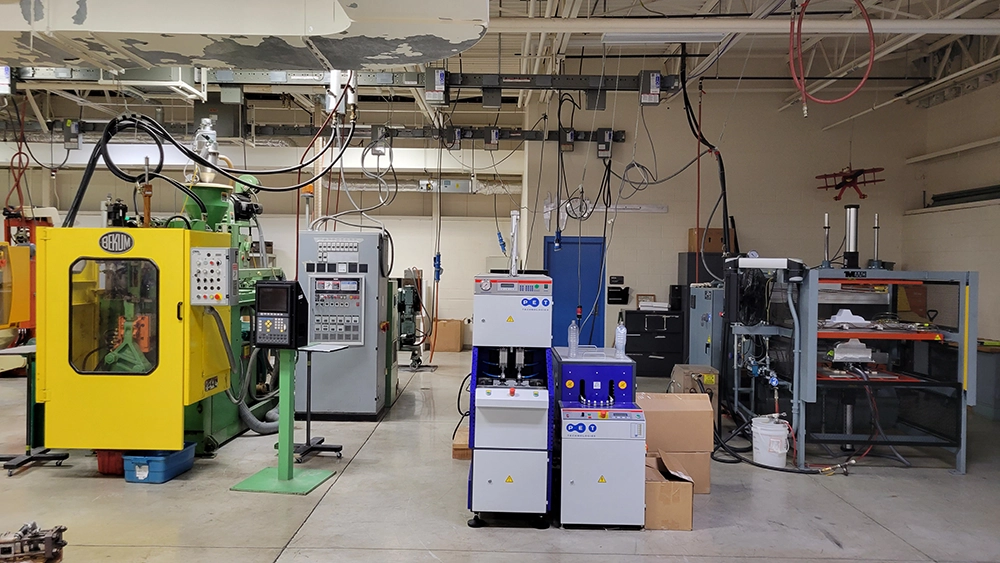
Ferris State University, www.ferris.edu, is a four-year public institution located in Big Rapids, Michigan. Marc Guske, program coordinator/associate professor, Plastics & Rubber Tech, School of Design & Manufacturing, provided information for this article.
According to the school’s website: “The Plastics and Rubber programs at Ferris State University offer a unique experience. All students enter a common program for the first two years. During these first two years, students are exposed to plastics materials, rubber materials, design, and processing for both rubber and plastics. Once the AAS graduation requirements are met, students can declare either Rubber Engineering Technology or Plastics Engineering Technology as their Bachelor of Science degree program.”
What does your institution offer in plastics-oriented certificates or degrees?
We offer a Polymer Materials Technology minor, an AAS in Plastics and Polymer Engineering Technology, and a BS in Plastics or Rubber Engineering Technology. Due to our small class sizes, students can come away with over 100 hours of solo injection molding machine experience.
How many students are enrolling in your plastics-oriented programs each year?
We aim for 48 students a year. The numbers decreased during the pandemic and possibly due to bad press about plastics. Our biggest recruiting tools are our unique lab facilities. We couldn’t offer field trip tours for the last couple of years, but they have resumed and we expect enrollment numbers to rebound.
What practical experience is required?
Students are required to do an internship for the AAS and BS degrees. Those are paid, so students get compensation plus experience. We facilitate companies in offering internships, but for the most part the students reach out directly. Companies alert me about open positions, and I alert the student body. And, we have career fairs each semester. Most students have a job offer as they are finishing their last semester of classes.
How is your institution partnering with the manufacturing community in your area?
Through our internship network, we have about 60 companies that take our students. We have good relationships with industry partners that donate lab materials, and we get equipment on consignment through our connections with big equipment manufacturers. We have some of the latest technology in our labs, as well as some older but still popular equipment. We just got a new Engel on consignment. The biggest supports we need right now are to raise awareness of both the industry and our programs, and it would be great to partner with some local manufacturing sites that bring in K-12 students for events like National Manufacturing Day.
How is your institution promoting these programs?
We hired a professional recruiter to engage more via social media. For me, when I can get a student on campus, show off our facilities and have a conversation, I have a very high conversion rate. Part of it is getting people to not think of plastics as a dirty word but, instead, to realize that we are the most sustainable material for most things.
What do you think should/could be done to get more students to enroll?
We need to network with high school counselors who can identify students who will thrive in a hands-on environment, who can think practically and who can feel confident working with large equipment.
Northwood Tech
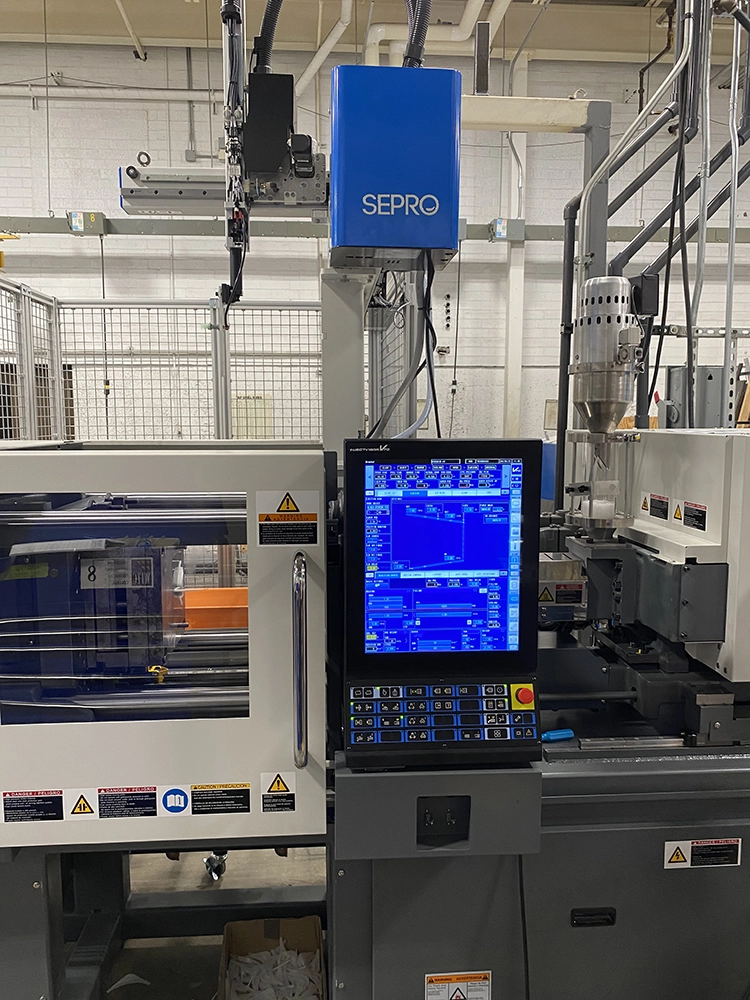
Northwood Technical College, www.northwoodtech.edu, is located in Rice Lake, Wisconsin. Northwood Tech’s Eric Lockwood provided information about the school’s offerings.
According to the Northwood Tech website: “Units of instruction include electricity, hydraulics and pneumatics; statistical process control; plastic mold design and blueprint reading; technical mathematics; basic tool room machine shop operations; and an overview of many of the plastic molding processes other than injection molding.”
What does your institution offer in plastics-oriented certificates or degrees?
We offer an Injection Mold Setup (Plastics) registered apprenticeship program, which is a work-based training model: 90% on the job training and 10% classroom. The apprenticeship allows apprentices to be onsite at the workplace most of the time, while upskilling through classes at the college. We enroll apprentices in the spring and fall semester. The number fluctuates; we average 12 apprentices.
Once they have finished their education, how quickly are those students getting hired?
As apprentices, the students already are working for an employer. Since the majority of registered apprenticeships are on-the-job training, it requires an employer to sponsor an apprentice into the program. There are opportunities for apprentices to advance in the company.
How is your institution partnering with the manufacturing community in your area?
Our local industry was key to starting the apprenticeship program in 2017. It started with one company seeking training for setup technicians and then expanded to other companies. To create a pipeline, companies that sponsor the registered apprenticeship program also support youth apprenticeship. Youth apprenticeship allows high school juniors and seniors to work for companies and explore career opportunities while also taking classroom instruction at their school.
What additional support do you wish you had for your programs?
Equipment is expensive, although we recently utilized a Department of Labor (DOL) Workforce Innovative grant to purchase a new mold press, robot, temperature control unit and conveyor. Through a bid process to purchase the equipment, QMC Plastic Machinery LLC, St. Paul, Minnesota, was awarded the bid. Its owner, Reed Qually, is very supportive of educational institutions having the equipment to meet the needs of the plastics industry. He donated equipment that enhanced what we can do with the new equipment that was purchased.
How is your institution promoting these programs?
Through face-to-face meetings with our industry partners. Our instructor works in the industry and has been instrumental in promoting the injection mold apprenticeship through industry connections. We market through social media, the college webpage and print media. We also make use of collaborative partnerships. I serve on area youth apprenticeship steering committees made up of high schools, industry members and economic development corporations.
What do you think should/could be done to get more students to enroll?
Continue to introduce more people to the career opportunities in the plastics field. That is why we focus on the bridges between youth and registered apprenticeship.
Pitt State
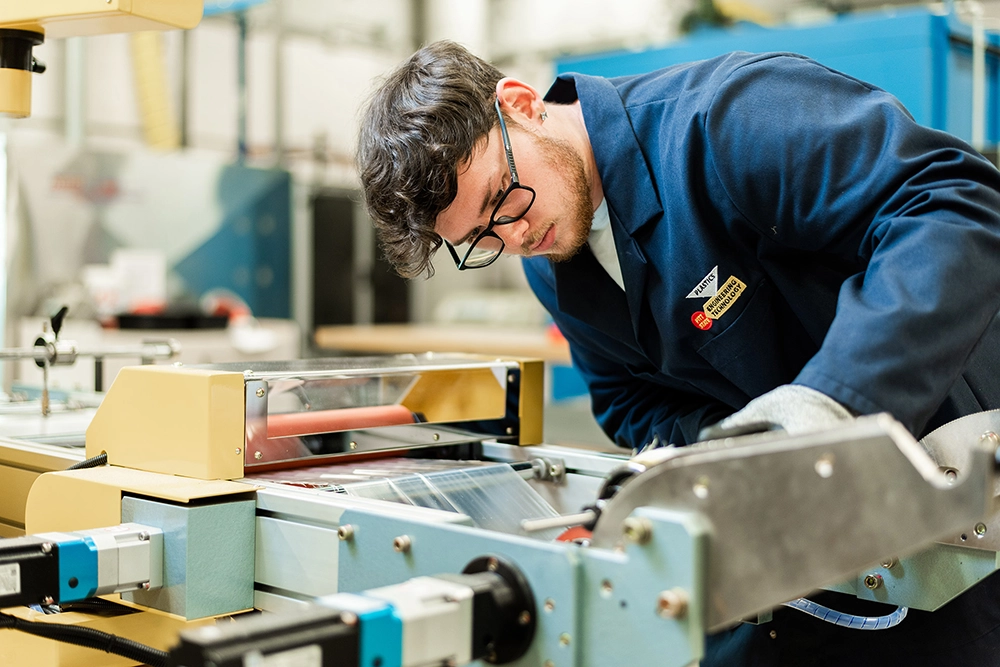
Pittsburg State University, www.pittstate.edu, is a four-year public institution centrally located in Pittsburg, Kansas. The University has a flat-rate, in-state tuition structure, with “in-state” applying to 32 states. Greg Murray, professor and chair of engineering technology, shared information about the Pitt State program.
According to the university’s website: “Pittsburg State’s Plastics Engineering Technology program provides students with detailed technical knowledge and the ability to hone their skills on state-of-the-art equipment… [The program] emphasizes detailed technical knowledge as well as real world application.”
What does your institution offer in plastics-oriented certificates or degrees?
The plastics program started in 1969 and has been ABET-accredited since 1979. We offer a two-year AAS in Plastics Technology, a four-year BSET in Plastics and a Masters of Engineering Technology with an emphasis on Plastics. We typically have 75 to 90 students in our program.
Once they have finished their education, how quickly are those students getting hired?
We have 100% placement for students who are looking for a job. Most students find full-time employment in the fall of their senior year at our Company Day recruiting event. Most graduates have two to three job offers to choose from at that time.
What practical experience is required as part of your programs? Internships?
We offer a two-semester capstone project during students’ senior year in which they work on projects that they may see in industry or work directly with regional companies on projects. We do not require internships; however, we do highly recommend them. Most students will complete one or two internships or work part-time with local plastics companies before they graduate.
How is your institution partnering with the manufacturing community in your area?
We have a Plastics Engineering Technology Advisory Council meeting once a semester, which includes companies from around the region. We also work with industry partners on student/faculty projects and research. Throughout students’ time here, they will have attended several company tours and have heard from several guest lecturers.
What additional support do you wish you had for your programs?
Like any technical program, we constantly are trying to keep up with the latest technology – which takes funding. We have received some grants in the past few years to help with updating our equipment, but it is a constant challenge to find funding.
What do you think should/could be done to get more students to enroll?
That is the magic question! We provide prospective students with a small scholarship when they visit our facility, and we give away over $80,000 in plastics scholarships each year… however, the real question is how to get them here. I believe that continuing to make students and parents aware of the industry while visiting schools is important. A lot of high school students do not realize that an education in plastics is even a possibility.
UMass Lowell
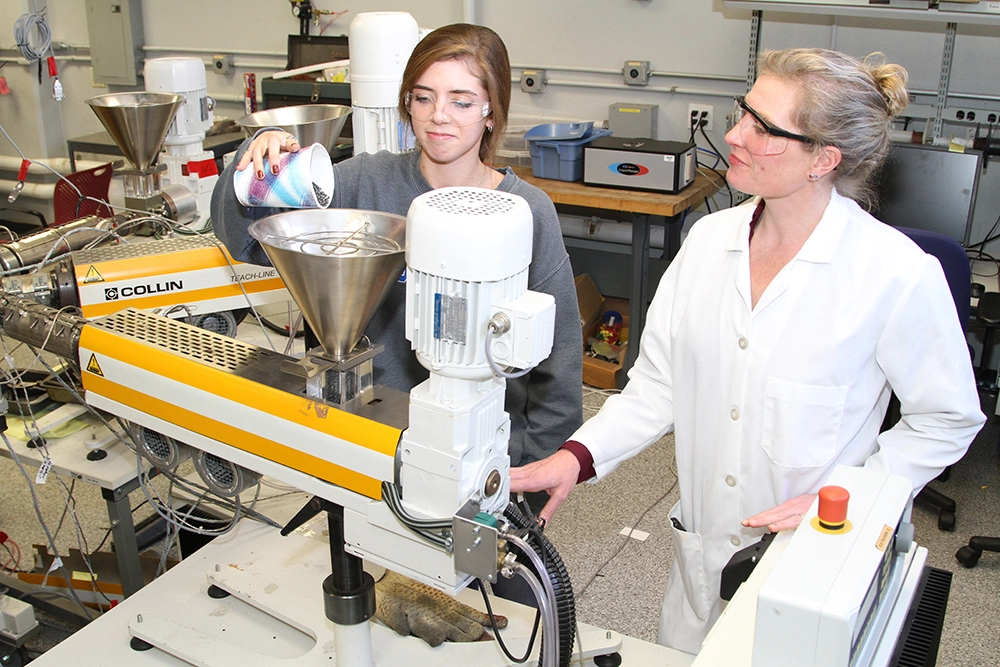
The University of Massachusetts-Lowell, www.uml.edu, is a four-year public institution located in Lowell, Massachusetts. Amy Peterson, associate professor and associate chair for Master’s Studies, was interviewed for this article.
From the university’s website: “Our programs combine hands-on laboratory experiences relevant to the industry with the fundamental theory in mathematics, science and engineering. Students are exposed to all of the major plastics manufacturing, design and testing technologies. The department has 20,000 sq. ft. of dedicated laboratory space that has recently been renovated.”
What does your institution offer in plastics-oriented certificates or degrees?
UMass Lowell offers an undergraduate major in plastics engineering, a MS in Plastics Engineering, a PhD in Plastics Engineering and six graduate certificates in plastics engineering including Elastomeric Materials, Medical Plastics Design and Manufacturing, Plastics Design, Plastics Engineering Fundamentals, Plastics Materials and Plastics Processing.
How many students are enrolling in your plastics-oriented programs each year?
A typical undergraduate class size now is around 30. Plastics Engineering MS enrollments typically are around 70 to 80, while PhD enrollments typically are around 35 to 40 and graduate certificate enrollments typically are around 25 to 35. Our undergraduate numbers are lower right now, in large part because recruiting undergraduates with no knowledge of plastics engineering into our program works best in-person and by showing off our laboratory facilities, which was curtailed during the COVID-19 pandemic.
Once they have finished their education, how quickly are those students getting hired?
Our students are very employable. If they are not already working, our students have jobs lined up upon graduation or are pursuing advanced degrees. Of students who earned BS Plastics Engineering degrees in 2022, 67% went to work in the industry and 31% continued their education.
What practical experience is required as part of your programs? Internships?
All of our degree programs include required laboratory courses, which give our students valuable hands-on experience in polymer synthesis, plastics processing and characterization. Our BS and MS programs also have optional co-op programs, which give students the opportunity to apply the knowledge they’re learning in classes to real-world challenges in a work environment, while also earning money. Nearly 100% of the undergraduate students participate in at least one co-op experience.
What additional support do you wish you had for your programs?
A major challenge that we currently face is the negativity surrounding plastics. We are committed to training the next generation of plastics engineers and performing research that can contribute to improving the sustainability of plastics processing and plastic devices, whether through new materials development, recycling, novel processing or a combination of these strategies. We would like to get the word out about how a plastics engineering education can help people be part of the solution for greater sustainability.