by Lindsey Munson, editor, Plastics Business
A high percentage of the American workforce represents the plastics industry. With so many in the trade, it is key for companies to place awareness, training and a cultural balance of safety and health at the forefront of their mission. It takes the dedication of every person, every day, whether in the front office or on the shop floor and production line to make safety a priority. In line with OSHA, MAPP and other key industry partners, companies can obtain valuable resources, training opportunities, personnel support, best practices and safety guidelines that cultivate a culture of, “Safety comes first!” The companies profiled in this article took safety to the next level through their best practices.
Augustine Plastics, Inc., Somerset, Pennsylvania
James Brown, president and CEO stated, “We were able to achieve this Gold level by a 100% unwavering commitment by ownership, management and employees at all levels across the company. The key, significant takeaways for achieving zero OSHA-reportable injuries and illnesses, not only in 2021, but since our April 2008 inception, is that our consistent pursuit of uncompromising safety is working successfully. That’s a notable 5,212 days as of today.” (July 22, 2022)
Shortly after Augustine Plastics, Inc.’s (API) April 2008 inception, ownership and management established official workplace safety protocols. Driven by monthly safety inspection walkthroughs of the entire facility to ensure that a safe working environment was being maintained and to identify and correct any potentially hazardous situations, API implemented new necessary safety measures and made adjustments to current ones to ensure continued safety standards were met on every level. In October 2016, API officially developed a Workplace Safety Committee and pursued certification from the Pennsylvania Department of Labor & Industry (PA DOL&I), achieving certification on February 16, 2017. In addition, API is OSHA-compliant, Tier II-compliant and DEP/EPA-compliant.
“We emphasize the importance of a safety culture and keep environmental health and safety a top priority across the company through successfully meeting the objectives of our Workplace Safety Committee’s mission statement. Our objectives are to create and promote a safe working environment for all employees, initiate and uphold an active interest in safety and assist in the overall effort to minimize the frequency of incidents throughout the company, identify corrective measures needed to eliminate or control recognized safety hazards and ensure that all mechanical and physical facilities required for personal safety and health are maintained with the highest standards,” said Randy Zimmerman, operations manager.
Along with members of API’s Workplace Safety Committee, they engage non-committee members in the monthly safety inspection walkthroughs, on a rotating basis, who learn about the focus areas and the reporting of any potential safety issues. The committee generates a report that documents and confirms that the current safety practices are in place and are working, and identifies any immediate actions that are required.
To maintain safety for all employees, API has numerous control systems in place. Examples include having members of the Certified First Responders Team covering all three work shifts, first-aid supplies and AEDs, personal protective equipment, two-hour rotation of operators to reduce physical and mental fatigue, updated fire/security alarms, fire protection equipment, personal protective equipment, machine guards, lockout/tag-out system and electronic card readers on all entrances. They offer specialized training as required on the handling, storage and disposal of flammable, combustible and hazardous material with clear labeling and all necessary safety data sheets. Members of their certified Workplace Safety Committee receive the required annual training credentialed by the Bureau of Workers’ Compensation, which at a minimum, includes the four areas of hazard detection and inspections, accident and illness prevention and investigation, safety committee structure and operation, and as of October 2021, substance abuse and opioid painkiller use.
In line with Augustine Plastics’ continuous improvement plan for workplace safety, the company upgraded its fleet of forklifts. To provide a visual warning of oncoming forklifts, Augustine Plastics added pedestrian safety blue LED warning spotlights that project an intense light on the floor. As an audible warning, the company upgraded its main material handling forklifts with a continuous beep alert system to not only sound during back up, but any time the forklift is on.
Brown proudly added, “We are very honored to be recognized by MAPP with this Gold Safety Achievement Award, and more importantly, are thankful that what we are collectively doing as a company has kept our employees safe.”
Nylacarb, Vero Beach, Florida
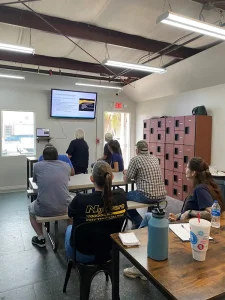
Nylacarb a family-owned business places safety and family at the forefront of its company mission. It is not lost on Nylacarb’s leadership and management team that their employees are working hard for those they love most, their family. “After all, they come to work each day because they are making a living for those who love them – the very least we can do as an organization is value their safety while they do so,” said Tatiana Cooley, marketing director and operations specialist.
Nylacarb has taken big steps over the past few years to revamp and restructure its safety program. With a safe and healthy work environment and a company culture of open dialogue, Nylacarb has been able to develop and release up-to-date health and safety standards through real-time information and interactions with employees. A key piece to open dialogue is an active email available to employees that directly notifies the management team of potential safety hazards, concerns and recommendations. Additionally, training new and current employees is an absolute necessity in meeting their safety measures and a valued part of why they have had success in meeting zero OSHA recordables. New employees are required to complete a 3-part virtual safety training program which is done through an online presentation that provides general safety information including health and wellness, first aid, PPE, fire extinguisher locations and emergency exit routes. One of the most influential parts of Nylacarb’s safety program is the monthly Safety Committee comprised of at least one representative from each shift, the maintenance manager, the safety director and key personnel from the administration/management team. Each month, the Safety Committee teaches a new safety topic during shift meetings. The safety briefings are an opportunity for Nylacarb to engage with their team, keep safety expectations top of mind and perform critical basic safety housekeeping practices at end-of-shift. Notably, the failure to perform end-of-shift duties can result in a point and write-up from management (Six points in a tri-annual period can result in the loss of an employee’s tri-annual bonus.).
Cooley shared, “Educating our employees on best practices is vital, but more importantly, getting everyone from top to bottom to buy in on the ‘why’ we choose safety first is what sets us apart!”
Plastikos Medical, Erie, Pennsylvania
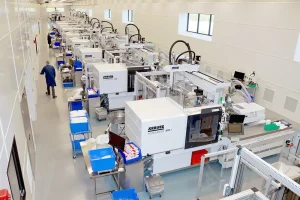
A mirror hangs in Plastikos Medical’s clean room that reads, “Meet the person most important for your safety.” Plastikos Medical has a culture that breathes safety. The mirror is the tipping point and is a simple way to give a good reminder to employees entering the clean room or walking by that safety should be everyone’s priority and responsibility.
Teaming up, Plastikos Medical and Plastikos have combined efforts in making the Safety Committee the best it can be and most influential across the company brand. This committee is made up of 20 employees and handles the majority of the safety concerns. Every month, Plastikos Medical and Plastikos kick off their in-person, all-employee meetings collaborating as a team on environmental health and safety topics as well as company-wide continuous improvement projects. A recent improvement project was digitizing the SDS log and all training was added to the main online training software.
The focus is not on a “quick fix” but instead on long-term solutions that will effectively benefit the employee and elevate the work environment. For example, an employee who operates a forklift took a concern to management. Within the same week, solutions were researched, which then ended with the purchase of mirrors and then properly placing them in blind spots throughout the warehouse and loading dock. Management also is proactive with investing in new equipment, recently purchasing an electric pallet jack to move heavier molds to the larger injection molding machines, eliminating the risk of an employee accident and unnecessary safety concerns. Plastikos Medical’s employees are the heart of their company so by opening up hours upon hours of training from molding managers and the HR manager completing OSHA 10 training to employee volunteers getting trained in first aid, CPR and AED they saw a year’s worth of success.
“I’m very proud of our Team,” said Danielle Bentley, medical molding manager. “Our culture promotes a safe, comfortable and clean environment where employees can express themselves freely to promote new ideas and troubleshoot areas that could be improved. Empowering employees to speak freely and encouraging a team mentality is huge when it comes to being safe, especially in a manufacturing environment.”
Bentley continued, “It is an honor to receive this award and it is a great reminder for Plastikos Medical to keep safety a priority and continue the hard work towards zero OSHA recordables for 2022.”
MAPP Announces Four Companies as Gold Safety Achievement Award Recipients
The virtual 2022 Environmental Health and Safety (EHS) Summit was held on April 27-28, where the Manufacturers Association for Plastics Processors (MAPP), Indianapolis, Indiana, announced the winners of the Safety Awards. The Safety Awards Program is comprised of two awards, the Safety Achievement Award and the Safety Best Practice Award.
Gold Safety Achievement Award
This award requires the organization to have zero recordable cases.
Augustine Plastics, Inc., Somerset, Pennsylvania
Nylacarb, Vero Beach, Florida
Plastikos Medical, Erie, Pennsylvania
PTG Silicones, New Albany, Indiana
Silver Achievement
This award requires the organization to have the lowest number of recordable cases.
Sussex IM, Inc, Sussex, Wisconsin
Honorable Mention
This award requires the organization to have the lowest incident rate.
Plastikos, Erie, Pennsylvania
Wise Plastics, St. Charles, Illinois
Commitment to Excellence
This award requires the organization to have a low incident rate and minimal recordable cases.
Hoehn Plastics, Inc, Poseyville, Indiana
Ironwood Plastics, Inc, Two Rivers, Wisconsin
Majors Plastics, Omaha, Nebraska
Stone Plastics, Zeeland, Michigan
Safety Best Practice Award
This award recognizes the “best practices” that an organization implemented to increase overall safety.
Automation Plastics, Aurora, Ohio
Plastic Molding Technology, El Paso, Texas
Trademark Plastics, Newark, New Jersey