by Liz Stevens, contributing writer
Plastics Business
The Manufacturers Association for Plastics Processors (MAPP) presented the MAPP Innovation Awards for the fifth year in 2019. The awards, established to recognize innovative solutions to common issues, focused on the following question, “How has your company instituted systems in your facility to make workstations safer, more ergonomic, more efficient and/or improve the organization?”
Over 20 final submissions were submitted for voting, and more than 479 industry peers voted to determine the winners. This year’s awards were split into two categories to recognize companies in different sales groups – specifically, those with annual sales under $15 million and those above $15 million. The winners were:
Under $15 million category
- First Place: Blue Ridge Molding
- Second Place: Wadal Plastics
- Third Place: Bruin Manufacturing
Above $15 million category
- First Place: Intertech Medical
- Second Place: Plastic Components, Inc.
- Third Place: Falcon Plastics – Lexington, Tennessee, location
These awards allow MAPP members to benchmark best practices among peer-level companies in the industry, and 20 of the submissions are shared in the 2019 Best Practices Book.
First place winners
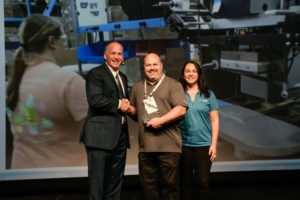
Blue Ridge Molding, first place winner in the under $15 million category, detailed its redesign of a workstation layout. The company revamped its original workstation layout – a linear flow in which five workers passed a product from its emergence from the press through assembly and to being boxed for shipment.
In the new layout, the product flow has been split into two streams of sub-assembly, with the output of the two streams merged for final assembly, packaging and boxing by a last, single worker.
Blue Ridge outfitted the new workstation layout with floor mats, task lighting, supply holders and custom-made tools. The company also created notebooks with clear visual instruction steps, and accompanied the instructions with completed product samples.
The company reported that the new layout reduced labor requirements, increased production efficiency, standardized work instructions, improved ergonomics and worker safety, and reduced both the footprint of the workstation and the amount of movement required by the workers.
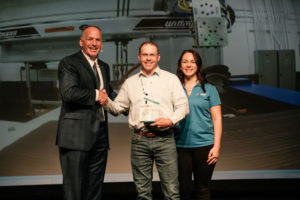
In the above $15 million category, Intertech Medical was voted into first place with its submission describing the creation of a new automated cell for producing and assembling a two-part item: a tray populated with 96 tiny tubes.
For this new business venture, Intertech estimated a production volume of 20 million tubes per year, or 212,000 individual tray and tube assemblies. When envisioned as a manual assembly process, the difficulty of hand-placing nearly 100 tiny tubes in each tray and the amount of time required for the task led Intertech to instead imagine an automated process.
Intertech’s innovation was to mold the trays in one pass, and then mold tubes with simultaneous automation to pick and place the tubes precisely into a waiting supply of trays. The company’s design includes a Wittmann Battenfeld 818 robot with end-of-arm-tooling with vacuum power to confirm part detection and place the tubes, and additional EOAT functioning to ensure proper seating of the tubes. The design also takes advantage of a RobotUnits conveyor and Mitsubishi PLC to control conveyor functions.
In addition to creating an operation that loads the trays with tubes in less than a third of the time that would be required for manual assembly, these medical industry products are produced with zero contamination and no DNA from human interaction. Robotic automation of this cell also minimizes part and mold damage.
Second place winners
Wadal Plastics took second place in the under $15 million category with its idea to streamline a molding job that uses precisely placed metal inserts for over-molding. Wadal innovated by adding a vision system to confirm correct placement of the metal inserts (and avoid tool damage), along with an automated gate trimming station, which also confirms that all metal inserts are present and automatically routes the sprue and runner into a grinder.
The company reported that its innovation has improved quality, reduced the need for supplemental inspection of parts and slashed production time.
The second place winner in the above $15 million category was Plastic Components, Inc. The company created a 20-cell lights out facility – including presses, conveyors, grinders and box fill systems – in a 122’x41′ footprint.
This facility is not only lights-out and very compact, it also is designed to minimize waste, optimize ergonomics, capitalize on standardization and improve efficiency.
The design incorporates automated box fill systems, a mezzanine above the presses from which material is supplied, RJG process monitoring, automatic press shutdown and an overhead crane system. A small crew visits during first shift to restock, make changeovers, and wrap and ship finished goods.
Third place winners
Bruin Manufacturing placed third in the under $15 million category with its Newton, Iowa facility, designed to be as lean and efficient as possible. Bruin created an operation with seven injection machines that operate 24 hours per day and 6 days a week, with only 1.5 employees.
All seven machines (Bruin’s proprietary hot runners) are fed raw material via a vacuum system that keeps hoppers full, and each machine feeds its finished products – with the help of automated box changers – toward a centralized cell to be inventoried, labeled and prepped for shipping. Bruin’s design at the Newton facility can be expanded with several more machines without the need for additional employees.
Placing third in the above $15 million category, Falcon Plastics (Tennessee) submitted two best practice examples for optimizing operations by adding cobots or robots to perform finishing and assembly at the press. In the case of a strap assembly, Falcon Plastics implemented a cobot to pare the number of employees required at a workstation and eliminate the need for transporting and storing WIP parts.
In another instance, Falcon Plastics added a Sawyer robot at the press to handle hot stamping during assembly, thereby reducing labor, ensuring higher quality and eliminating the need to keep WIP inventory on hand.
Wide-ranging innovations demonstrated best practices
The 20 submissions for this year’s MAPP Innovation Award covered a variety of innovation categories, ranging from targeted improvements to sweeping holistic designs. Here’s a breakdown of the innovations and companies.
Innovative Components shared the details and benefits of its cleanup/organizing projects and its adoption of safety vests for anyone who visits the production floor.
Cosmetic Specialties and Noble Plastics offered submissions based on designing superior storage systems for CNC milling tools, and press-side tools and equipment, respectively.
Four companies – Falcon Plastics (South Dakota), Intertech Plastics, Microplastics and Par 4 Plastics – submitted best practices involving the creation of or changes to production or assembly line systems.
PMC Smart Solutions and Wadal Plastics shared insight about incorporating vision systems that improved the companies’ production quality.
Six companies reported the positive benefits of adding cobots to their operations – Falcon Plastics (Tennessee), PolyFlex, Steinwall, Techniplas, Viking Plastics and Wadal Plastics.
Alwin, Blue Ridge Molding, Techniplas and Wisconsin Plastics were the four companies that shared their ingenuity in changing workflows or workstations.
Intertech Medical’s submission revolved around designing an automated workstation.
Both Bruin Manufacturing and Plastic Components Inc. shared details on how holistically designed facilities were imagined, designed and realized.
Learn more: www.mappinc.com