
By Lindsey Munson, editor, Plastics Business
Located in Auburn Hills, Michigan, Champion Plastics has served as a custom injection molder for the automotive, motorcycle and industrial/commercial markets for more than 40 years. Founded by three-time Olympic speedskater and 1964 gold medal winner Terry McDermott, the company has continued its winning ways under the leadership of current President Jeff Ignatowski, Vice President/Director of Operations Matt McDermott and Senior Consultant Mike McDermott. Champion Plastics recently was recognized with an industry award for its innovative use of automation to increase production efficiency and reduce operator hand work on a high-volume automotive program.
Big Idea, Big Results
In early 2022, Champion Plastics was awarded a new high-volume program for General Motors. The program was a thermoplastic vulcanizate (TPV) molded component, accompanied by a pressure-sensitive adhesive tape that is applied to the part post-molding. The component is molded in a 2+2 family tool with left-and right-handed parts, and due to the TPV’s low surface energy, an adhesive promoter from AdPro™ needed to be applied so the pressure-sensitive tape adhered properly.
Initially, the program launched with six highly skilled operators. An operator separated the left-and right-handed parts, two operators applied the adhesion promoter (and struggled to maintain pace due to the volume output.) and three operators applied the tape.
This lack of efficiency could have continued indefinitely, but the leadership team at Champion Plastics approaches production differently than many companies, with an emphasis on understanding the process and doing the job first-hand. Ignatowski shared, “I did a presentation at the MAPP Conference called ‘Walk a Mile in Their Shoes,’ and the premise of it was getting out from behind the desk and onto the shop floor – not just to walk around and have conversations but to truly put yourself in an operator’s role. I’m a big believer in a hands-on approach to see and experience what the challenges are and what works well in the process.”
Ignatowski took a turn on the assembly line – and quickly realized the process was less than ideal. The adhesion promotor was a smelly, sticky adhesive. “When using the adhesion promotor on the assembly line, operators had to have fans on, and after personally completing the task, I was light-headed and felt the process was miserable,” he said.
Other realizations included the assessment that the operators’ jobs on the assembly line added a significant amount of labor in an extremely fast-paced environment. “It was time for the management team to step in and start working on the problem,” Ignatowski said.
Still, in the early stages of the program, Champion Plastics brainstormed and reworked the problem areas, conceiving an idea to replace the existing manual adhesion promoter operation with an automated plasma treating process. This treatment would be done inline with the injection molding cycle, using an existing 3-axis robot and end-of-arm tooling (EOAT).
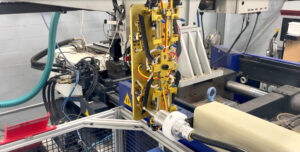
Years ago, Ignatowski worked for a plastic decorating company that used plasma technology to treat low surface energy plastic prior to paint application. Plasma treatment works by removing surface contamination and creating bonding sites to improve adhesive performance. Pulling from his experience, he said, “It clicked that the adherence issues were similar, whether applying paint or tape, and the lightbulb turned on! The concept is the same, and the component could be treated with plasma.”
Enercon is a Chicago-based plasma supplier that manufactures industrial, institutional and professional cleaning and maintenance chemical products and product delivery systems. In partnership with Champion Plastics, Enercon conducted a trial period using production parts and the pressure-sensitive tape. “We realized quickly that we’ve got something here,” said Ignatowski.
In addition to assisting in the plasma treating process, the EOAT also would step in to recycle components from the runner and cavity. This, in turn, eliminated three full-time operators and an offline operation. But process improvement didn’t stop there. While in the design and engineering phase, it came to the operators’ attention that the side of the part that needed plasma treatment was on the cavity side of the tool, so the part would need to be rotated prior to treatment. Responding to this issue, Champion Plastics realized a full automation solution needed to be implemented for this program to find success in labor reduction, product quality and return on investment (ROI).
Champion Plastics formed a second partnership with JH Automation, Port Huron, Michigan, a company that specializes in turnkey automation and process control. An EOAT grabs the part, flips it over and then positions it for the addition of the plasma treatment to the component. “It works like a charm and is just beautiful,” Ignatowski shared.
Through this automation innovation, Champion Plastics maximized productivity by eliminating labor resources and reallocating them to value-added operations; minimized operating costs with the elimination of the adhesion promoter; and removed an additional work-in-progress step – all while improving product quality. All of this is achieved with a fully automated process that is repeatable, measurable and reliable rather than operator dependent.
Champion Plastics reported a substantial return on its investment. An initial capital expenditure investment of $45,000 offset annual labor costs of $150,000. Over the life of the program, savings could reach up to $900,000.
Following the success of this innovation, Champion Plastics has visions for plasma treating automation in future jobs. Ignatowski said, “With existing jobs, the transition is layered with approval process delays, but for new jobs, the push is on for plasma treating. It allows our pricing to be more competitive, and it’s really neat to be making an innovative impact and leaving a footprint that protects the environment and operators.”
The future is bright, and Ignatowski said this initial automation step in preparing the surface prior to adhering the tape to the part will lead to more innovations on the plant floor. “The next step will be fully automating the production line by applying the tape with robotics, rather than finishing with a manual process,” he explained. We’re so proud of the Champion Plastics team and those that partnered with us. Innovation is a team effort!”
2022 Innovation Award Winners
Automated Manufacturing Solutions
In early October 2022, the annual Benchmarking & Best Practices Conference was held in Indianapolis where the Manufacturers Association for Plastics Processors (MAPP) brought together over 500 industry professionals. With networking and keynote speakers at the forefront, one of the coolest parts of the conference was the presentation of the eighth annual 2022 Innovation Awards, sponsored by AMCO Polymers, where winners were recognized on stage and applauded by their peers.
MAPP’s core value and mission are to connect and share innovative best practices and methods throughout the membership. Each year, MAPP diligently puts together a leadership committee made up of individuals from the membership, who select the theme for the Innovation Award, review and evaluate every submission and then narrow it down to the top six finalists. From there, the entire MAPP membership is sent the top six submissions where they are asked to vote and select the award winners – plastics manufacturing is an industry with all hands on deck!
The 2022 Innovation Award theme the leadership committee chose was automated manufacturing solutions. A vital and evolving topic of the past year for many processors and ultimately 23 plastics manufacturers put their boots on the ground and dove into the innovative process. From ideation and project development to testing and market integration, candidates put forth automated solutions that benefited front-line workers on the manufacturing floor, drove supply chain access, created partnerships between suppliers and processors and fostered overall facility improvements both internally and externally.
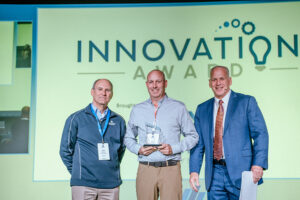
Champion Plastics won first in the Less than $15 million category for the 2022 Innovation Award with its submission on “Plasma Treating Automation.”
Jeff Ignatowski, president of Champion Plastics, was present when his company’s name was called and awarded the first-place prize at the MAPP Conference. “We heard ‘Champion Plastics’ over the microphone and were stunned because the company has always flown under the radar in the plastics industry. This award is the ultimate in respect because it’s an award voted on by all plastics processors – it gave us all a sense of pride!”
He continued, “There were so many innovative entries, I read them and voted as part of the MAPP membership. Following the award ceremony, we immediately shared pictures with the plant and team back home!”
Congratulations to the award winners at the 2022 MAPP Benchmarking & Best Practices Conference.
Greater than $15 Million in Annual Revenue
KW Container, Troy, Alabama
Beacon Engineered Solutions, Alexandria, Minnesota
Crescent Industries, New Freedom, Pennsylvania
Less than $15 Million in Annual Revenue
Champion Plastics, Auburn Hills, Michigan
Noble Plastics, Grand Coteau, Louisiana
Natech Plastics, Long Island, New York
More information: www.mappinc.com