By Liz Stevens, writer, Plastics Business
With thousands of manufacturers in the US, there are bound to be common quality issues faced by plant managers. There also are bound to be common-but-overlooked ways, as well as uncommon ways, to address those issues. Here are a few ideas for tackling quality issues; they might be just the ticket or they might be food for thought that will spawn an entirely new quality control approach.
Cleanroom Alternative
For some production jobs that call for a cleanroom, rubber manufacturers might benefit from thinking outside of the box. Instead of brick and mortar for a hard-wall cleanroom, how about a mobile version that can be moved from work cell to work cell?
A mobile cleanroom can be constructed with a tube steel frame on casters, clear vinyl curtain walls, a plastic strip doorway, ceiling tiles for a roof, light fixtures and fan-powered HEPA filters for a positive-pressure HVAC system.
- Mobile rooms do not take the place of all permanent cleanrooms, but they are a flexible option that can work in some situations and can be especially useful for secondary operations.
- A mobile cleanroom has low complexity and high flexibility when compared to a traditional cleanroom and can be constructed in days or weeks. A mobile cleanroom with a simple design costs much less than permanent construction while delivering more flexibility.
- The cost of the HVAC equipment will be the biggest variable and will depend upon the ISO class standard that must be met.
The only obvious downside is that manufacturers enjoy a much higher level of control over a traditional cleanroom as compared to a mobile counterpart.
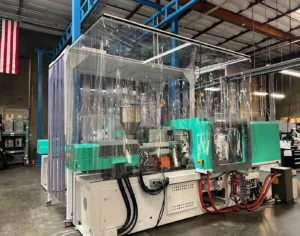
presentation by Westec.
A frame on casters means that the cleanroom can be moved to surround a single production machine or part of a machine, to shroud a critical assembly line or to contain an entire production line.
What to keep in mind: Seek a mobile cleanroom manufacturer that can build to spec to meet certifications; consider how to maintain the hygiene and integrity of the room, as well as maintenance of the HVAC system; factor in the need for HVAC that meets ISO standards and for particle count equipment to confirm the HVAC capacity; and remember to plan for training/protocols specific to the nature of a soft-wall cleanroom.
Haven’t Tried Computer Vision Yet? Take a Look
While it is hard to beat the human brain for breadth of knowledge, imagination and adaptability, a human brain tasked with performing visual inspection over and over all day long inevitably will experience fatigue, lose concentration and eventually make mistakes. Some sources cite an up-to-30% failure rate when humans attempt to catch quality defects, and poor quality control that leads to high scrap rates can take a big bite out of a manufacturer’s revenue.
- A computer vision inspection system paired with a robotic arm consistently can pick up parts, position them precisely to scrutinize and capture images from multiple angles, and assess the parts’ quality at multiple points simultaneously with superb high-resolution vision.
- Vision-enabled robotics simply don’t get tired, get distracted, get bleary-eyed or slow down. And they have an unmatchable knack for recognizing defective similarities and patterns – machine learning – to help guide design and production improvements.
Considerations for implementing a computer vision inspection system include choosing the correct lens for the size of the part being scrutinized and installing the proper lighting for illuminating a matte or shiny, an opaque or transparent, or a smooth or textured part and for revealing the tiniest flaws that may occur. - The software managing the system must be capable of collecting and storing visual data and able to use machine learning and number-crunching needed for this part or that certification or those customers.
- Each inspection configuration will be put through its paces for a validation test – fed a large number of parts with a known number of variable defects – to ensure that the machine catches as near to 100% of the defects as possible.Vision system vendors are ready to customize solutions and construct systems that meet plastics processors’ every requirement.
What is Leaner than Lean? 2 Second Lean
“It’s better to start small and consistent than large and inconsistent.” So says Paul Akers, author of “2 Second Lean,” who preaches the good news that it is not necessary to embrace the entire lean discipline and all of its rules and principles.“2 Second Lean” simplifies lean into concepts that the entire manufacturing plant’s workforce can understand, embrace and use. Implementing a scaled-down version of lean – just a few essentials – can offer a real payback, and smaller bites of lean are easier to grasp and implement.
- A mantra of “2 Second Lean” is empowerment; rather than empowering only designated problem solvers – aka management – to make helpful change, empower everyone on the plant floor and in the offices to make the little changes that add up to big improvement.
- Morning meetings, during which all employees learn about the company’s financial state, its latest successes and its biggest challenges, can be very brief but immeasurably valuable. With an overview of the company’s health in mind and empowered to “fix what bugs you,” employees at every level can walk the plant floor on the hunt for little problems that can be fixed with small improvements.
Improvement examples include organizing tool areas with the “a place for everything and everything in its place” mindset or standardizing how a process is done so that more consistency leads to less error and scrap. For a job with a learning curve for newbies, how about making a short video, uploading it to YouTube and posting a QR code at the workstation so employees can scan the code, watch the video on their phones and then get to work? - Along with empowerment, “2 Second Lean” depends upon employee engagement. Respect each individual’s value, and offer them chances to learn, grow, advance and teach.
- Engaging and empowering workers often helps cultivate a company culture that keeps veteran workers on the payroll and attracts new employees.By introducing “2 Second Lean” and inviting everyone to climb aboard as a constructive critic and changemaker, manufacturers can make big gains. n
This article was based on ideas that were shared at the 2023 MAPP/ARPM Engineering & Quality Forum on April 20-21, a veritable breeding ground for innovation. Thank you to the presenters, including “Master Class – Mobile Cleanroom,” by Rob Zimmerman, Westec Plastics; “Why Computer Vision Systems Beat Human-Based Inspection Every Time,” by Ed Chan, Mandy Dwight and Nick Keyes, Rapid Robotics; “Master Class – 2 Second Lean Journey,” by Shawn Gross, Viking Plastics.
More information: ww.mappinc.com/events
Reprinted with permission from Inside Rubber (www.arpmince.com).