By Marcella Kates, director of marketing, MAPP
While the resin shortages are affecting supply chains all over the world, one Indiana molder’s venture into repelletizing scrap materials turned out to reap rewards for the company and its customers.
Metro Plastics Technologies is a custom injection molder in Noblesville, Indiana. Metro believes in a commitment to utilizing its resources in the most responsible way. In the spring of 2020, the company put its money where its mouth was with that commitment and learned how to repelletize scrap materials.
Ken Hahn, president of Metro Plastics, said about the equipment that was required: “We were not exactly sure how to accomplish this, so we bought a small lab extruder and pelletizer, and then made our own water bath. After some failures and experimentation with different speeds and temperatures, we were able to master several types of materials. We then quickly upgraded to a 2½-inch extruder, which included an industrial water bath and pelletizer.”
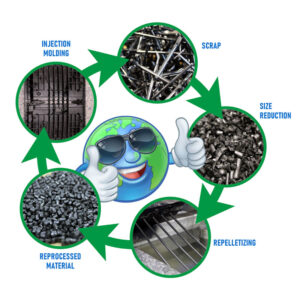
This turned out to be a fortuitous venture, as at the time no one knew of the looming resin and supply chain crisis that was to define the last quarter of 2020 and most of 2021. Metro’s dedicated materials team now specializes in reprocessing scrap material into secondary, non-critical parts, leaving a zero-scrap footprint and no shortage of resin.
Metro started with re-using its own scrap materials, while also stocking up on some resins when prices fell in the summer of 2020. This two-part strategy allowed the molder to operate without having to stop any lines for their customers and ensured the company would never run out of resin.
This internal venture then turned outward as Metro reached out to its customers to offer this service. The company now has two customers using Metro’s repellitizing expertise. One customer has asked the company to run the molded parts after repelletizing the scrap, and for the second, the customer’s repelletized resin is sent back for use in the customer’s own facility.
Reusing the scrap this way has provided a new advantage for Metro when selling to new customers, as the company tries to lead the way in green initiatives. Through the reprocessing of these scrap materials, Metro strives toward a zero-impact ecological footprint.
Hahn explained, “Although it is not a profit center, we are comfortable in the process now to know we are not throwing money away when a job does create scrap. In addition, it allows us to effectively use our recycled scrap efficiently. We feel it is the right thing to do.”
Metro has led the way with this unique idea to learn, improve and advance the company. The efforts have resulted in no shortage of resin, being a green company and saving its customers money in the end.