By Liz Stevens, writer, Plastics Business
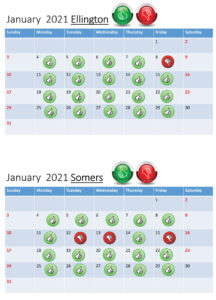
“What’s the score?” That question, asked by sports and game fans worldwide, reveals a lot about the human tendency toward competition and excellence. Whether it applies to professional sports, Olympic athletes, school sports or TV game shows, we crave knowing who scored the most and who won the match. We are a competitive bunch, and we like to be on the winning team.
The propensity to excel and to keep score has been tapped for training in manufacturing. Some plastics manufacturers have adopted gamification in their own training, and others encourage friendly competition between departments or shifts of workers for a variety of reasons. In Connecticut, Dynamic Molding Technologies (Dymotek) has tapped that competitive spirit as a way to improve the quality of its production output.
Dymotek offers engineering, injection molding, liquid silicone molding, assembly and fulfillment in two Connecticut locations – Ellington and Somers. The company spans 83,000 sq. ft. for its operations and boasts ISO 9001:2015 and ISO 13485:2016 certification. Dymotek operates a clean, bright production environment that includes the latest in automation and robot-facilitated manufacturing techniques, so it is no surprise that the company also is forward-thinking in its QA approach. Dymotek found that competition could strengthen and solidify the quality assurance for the products it produces. The company’s senior quality engineer, Craig Swanson, shared how the gamification of QA at Dymotek came about.
Dymotek’s QA initiative, called Quality Win/Loss, began at the end of 2019. The idea for the initiative arose after analysis by the Quality Assurance department revealed that product defects were being missed by Operations, only to be found by the Quality department.
“At Dymotek, the Operations department owns quality; they own the quality of the product,” said Swanson. While the QA department does inspect product, the Operations group first does its own series of inspections to identify problems during and after manufacture. “Our Quality department auditors inspect the product just prior to shipment,” said Swanson. Finding product issues at this point means that a problem has gone unresolved during manufacturing and resulted in a quantity of defective products – which certainly may disrupt the shipping schedule.
Further investigation about the missed defects revealed that misunderstandings in Operations about the sometimes confusing criteria for identifying product as acceptable, in need of rework or to be relegated to scrap. To address the misunderstandings, the Quality department clarified and increased its communications to Operations, then began to check for improvement and report the findings via the Quality Win/Loss initiative.
“We implemented Quality Win/Loss for both the Ellington and the Somers facilities,” said Swanson. A product issue that is found by Operations and remedied before any product reaches the warehouse is not counted for Win/Loss, but a poor ranking can stem from errors or oversights by Operations, such as incomplete paperwork or missed inspections. “If Quality found an issue during its inspection, the plant location got a thumbs down rating. We would track this daily, so each building had either a thumbs up or a thumbs down for each day.” These ratings were communicated to teams at both locations.
The fact that the company has two locations – in Ellington and in Somers – can create communication and coordination challenges but having two facilities also creates a natural division and the potential for good-natured rivalry. “As we began this initiative, we would communicate during our morning meetings the quality results for the two plants,” explained Swanson. “This progressed into a healthy, friendly competition between the plants. It was nice to see this develop naturally and not as something planned and injected into the culture.”
Frank Fasano, the company’s quality director at the time, came up with the idea of marking each location’s win or loss on a calendar located in each facility’s War Room with an actual thumbs up or thumbs down sticker.
The competitive spirit between the two locations ramped up organically. “This was happening because this information was shared not only at the morning meeting but also shared at the shift change meetings,” Swanson said. “Every shift in every building got to see how their building was doing and what their quality issue was.”
The initiative and the competition have yielded dramatic results. “There was constant communication with all shifts in both buildings about the non-conformances we were seeing and how we could better correct them,” Swanson stated. “And, at the same time, we were able to bring the quality issue trend down. We started seeing the trend of thumbs down drop drastically. At the beginning of 2020, we were averaging 14 to16 thumbs down per month for both facilities. In May of 2021, we have had a total of five thumbs down. That’s a good thing.”
That is a very good thing, and Dymotek achieved it with the wholehearted help of its workers, aided by a little bit of friendly rivalry. “Now that we have had this initiative for a year and a half,” said Swanson, “we are beginning to combine the Win/Loss of both facilities and report it as a whole. We still identify the facility in which the issue was found; however, the focus now is on communicating that while there are two facilities, we are all Dymotek. The friendly competition is still alive, as each facility works hard not to be the one that causes a thumbs down.”
As evidenced by the successful QA initiative at Dymotek, innovative manufacturers can turn “what’s the score?” into a win-win at their operations by introducing good-natured challenges and friendly competitions.