by Shane Vandekerkhof, Global Training & Education Integrator at RJG
Hold speed or hold velocity? How many machines today have it, and how does it affect the process? The machine controller input of hold velocity started to become more and more prevalent with the onset of electrically driven molding machines. The setting tells the machine how fast to move the screw during second stage. But, and this is a big but, second stage is a pressure-limited portion of the process. Velocity control can’t exist on a pressure-limited portion of a process. So how effective is the speed setting then?
The molding machine will use the speed that is input into the machine controller only until the set second stage pressure has been reached. Once the second stage pressure is reached, the screw slows down and may even eventually stop. This velocity input is seen as a matter of response time. The setting is telling the machine controller how fast to get to the second stage pressure setting.
The question becomes, “Does this setting impact my process?” The answer to that question is simple: Yes. Accompanying this article are a couple of graphs that represent first, the injection pressure profile, and second, the part weight. These are correlated to seven different second stage velocities starting at 5 ccm/s up to 35 ccm/s, moving in 5 ccm/s increments.
In figure 1, the slowest speed is represented in orange. It shows a large droop in the injection pressure profile after transfer has been reached. This occurs because the cavity is short at transfer, and it takes a period of time before the cavity completely fills and starts to pressurize. The resistance in the cavity now is pushing back on the screw, and the second stage pressure setting is reached and stabilized. As the second stage velocity is increased, the droop gets smaller and smaller, and the time it takes to reach the second stage pressure setpoint gets shorter and shorter.
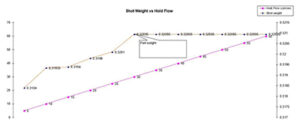
In figure 2, part weight is plotted against the second stage speed setting. The part weight is continuing to rise until 30 ccm/s is reached. At this time, any additional second stage speed has no influence on the part weight. This is the sweet spot for where the setting should be set – at a point where the final part weight is no longer influenced by the second stage speed.
Remember to think about what is happening to the plastic and to parts during this time. This is one of the most influential periods of the process for setting dimensions on the part. The slower the speed and response are, the slower the parts are being packed out and the slower the material is allowed to cool and solidify.
What about other machines?
When scheduling a mold in several different molding machines, it will be important to understand how each of those machines reacts to the second stage speed setting. Just because 30 ccm/s works on machine four doesn’t mean the same response will come from machine 12. This could be due to different machine makes and models, ages of the machines, hydraulic vs. electric machines, etc. There are too many things to list that could contribute to the difference.
Some machines don’t have an input for second stage velocity. In this case, the molding machine typically will use the last fill speed input on the machine controller. If that setting is slow, then the second stage velocity also will be slow.
Other influences
Besides the second stage speed setting, the size of the fill-only part also can contribute to the droop, or slow response. If the fill-only part is 60% full at transfer instead of 98% full at transfer, then it will take more time for the cavity to fill out and pressurize. When conducting this study, the parts need to be 98% full at transfer to eliminate that as a potential cause in the response. Make sure we are only the influence of the second stage speed velocity on the process is measured.
When trying to produce the most repeatable parts in the fastest, most repeatable time, the second stage speed setting is an often-overlooked influence on the process. Knowing how each machine responds to this input is one more step toward being better than the next molder.