
The MAPP members that earned recognition at the 2023 MAPP Innovation Awards did so with a focus on automation. Plastics Business checked in to learn the details from two MAPP members whose innovation submissions rose, like cream, to the top. Their solutions included a diverse array of tools and technologies, including robots, cobots, feeders, funnels, hoppers and air power.
Falcon Plastics, Brookings, South Dakota, is a mid- to high- volume custom injection molding and custom blow molding operation serving customers since 1975 in the agriculture, automotive, construction and industrial, electronics, medical, office products and recreational sports markets. Hansen Plastics Corporation, Elgin, Illinois, offers custom plastic injection molding, engineering and design, inventory management, insert molding, multi-material handling and decoupled molding for the appliance, automotive, life safety, fluid movement, transportation, construction and agriculture markets.
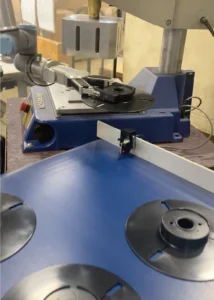
Falcon Plastics’ Cooperative Automation
Falcon Plastics earned a third-place award in the labor solutions category at the 2023 MAPP Innovation Awards for automated processes at its Brookings facility handling parts removal from a mold, degating and welding parts together. The company achieved this by combining a Sepro press top robot, a degate station, a UR cobot and a Branson ultrasonic welder. The result is automation of a large assembly part job that originally required a full-time operator, and which now can be completed with just one-quarter to one-half of the operator’s time, freeing up the operator and the press, too, for other valuable work.
This work cell produces plastic spools for cable or wire by molding two sets of parts – male and female – that will be joined as the final piece. Falcon added a Sepro press top robot with vacuum cups on the EOAT and a pneumatic gripper. The robot removes both pairs of molded parts from the press and moves them to a degate station where the runner is clipped. The robot then places the part pairs on a conveyor that transports them to a UR cobot. The cobot picks up a part pair, places them in a fixture and triggers a Branson ultrasonic welder. The cobot then removes the joined pair of parts from the welder and drops the finished product into a tote for packaging by an operator.
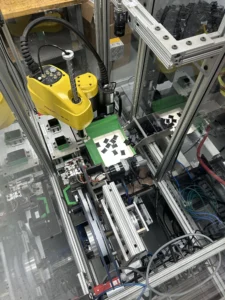
Falcon’s Kyle Banks described the programming that was required to set up the robot and cobot. “The programming itself was not difficult for either robot in general,” he said, “but like with any project, it had its own challenges. The hardest part for Falcon to program was indexing the conveyor so that the cobot could grab the first and second set of simultaneously molded parts from the same location.”
With a robot feeding two sets of spool parts to the cobot, some cycle time refinement was required to keep the robot from feeding parts to the cobot too quickly. “With the way we had the inputs and outputs communicating between the two robots,” said Banks, “timing was not a huge issue, but we did have to work at getting the cycle time down on the cobot, so we did not have to add extra cooling time to the part cycle.” The UR cobot activates the Branson ultrasonic welder through a nine-pin connector cable. “This cable takes the place of the cable that normally would be coming from the two-hand tie down at the base of the welder,” said Banks.
One of the few challenges posed by this automation installation was to make this work cell’s equipment easy to set-up and break down because the cell handles more than one job. “Since this set-up needs to be taken down and set up once a month,” Banks explained, “we had to come up with a solution to make redeployment easy and repeatable. We decided to use female-threaded anchor bolts to locate and hold both the welder and the cobot into place. They have worked well, and they also keep things from getting misaligned.”
A typical order for the spools at this work cell is 10,000 pieces. Prior to automation, it took 70 hours to complete an order because labor constraints allowed for only four to six hours of runtime per day. The result was that each order took 11 to 17 days to complete, keeping everyone hopping because another order for this item was bound to come in again soon. Post-automation, the operator’s time for this job was slashed from one operator to a quarter. For switching equipment out between jobs at the press, set-up time is one to one-and-a-half hours.
Falcon Plastics also was recognized for submitting a noteworthy labor solutions entry that appears in the 2023 MAPP Innovation Award Best Practice Book. This solution, implemented at the company’s Madison facility, automates the prep and application of cut lengths of Poron™ foam onto injection-molded slide-like substrates. Falcon puts an Asyril Intelliflex feeder, a FANUC 2D vision-guided SCARA robot and two vision systems to work on this project. Falcon’s Adam Rhodes gave insight into how the assembly automation was accomplished.
In this work cell, an Asyril Intelliflex feeder presents injection-molded “slide” parts to a FANUC 2D vision-guided SCARA robot for picking. “The Asyril Asycube,” said Rhodes, “is a part-feeding system that uses three-axis vibratory technology to separate and orient the parts for robot picking. It uses a camera about two feet above the Asycube along with backlighting to determine how many parts are on the table, to gauge their position on the table and to see how they are oriented.” The vision system sends signals to the Asycube to vibrate the slide parts into an optimal position for the robot to pick up. It also sends coordinates to the robot of parts that are ready to be picked.
As the injection-molded pieces are being prepped for pickup, another automated servo foam processor is slicing slide-sized pieces from a roll of Poron™ adhesive-backed foam and making each one available to a FANUC SCARA robot. The robot then places the slide onto the precut foam piece. “Accuracy of placement,” said Rhodes, “is monitored by a Cognex vision sensor located in the cell underneath the station where the foam and slide are joined. The robot brings the assembled slide over to the vision sensor for a quality inspection.” Good parts are dropped into one chute while rejects go into another chute.
“Placement of the foam on the slide,” said Rhodes, “typically holds a tolerance of +/- 0.01 inch. However, the main quality challenge we have faced stems from the foam material itself. We’ve found that certain portions of the foam rolls can be out of specification, which isn’t always detectable during the initial quality control process (IQC). Despite this, our average reject rate remains low at 0.6% per 50,000 parts, and about 90% of these rejected parts can be successfully reworked.”
Rhodes offered insight into how to tackle a work cell automation process. “Start with the finished product in mind and work backward,” he said. “Create firm expectations for the desired outputs and then identify the variables. From there, do research and figure out how best to tackle the process.” Rhodes knew that this machine had to be able to run four different part variations, with the option to add even more similar jobs with minimal effort; so, accommodating this requirement was baked in from the start. “Our changeovers needed to be simple so they could be performed by anyone,” he explained. “And the customer for this job has some fairly tight tolerance expectations, so we knew any process would need 100% inspection on the finished goods.”
The challenges inherent in this automation implementation – imagining, designing and fine-tuning the innovation – included learning how to use an Asyril Asycube and its vision guidance features. “The feeder and vision system was a first for our facility,” Rhodes said, “so figuring out the intricacies and how to program and calibrate the system created a learning curve.”
The payoff for this automation project was three-fold: an operator’s skills were freed up to focus on other valuable tasks, the placement of foam onto the slides now is more precise and consistent, and a secondary inspection prevents any out-of-tolerance parts from slipping through. The innovation is designed to handle four different types of slide/foam combinations, and the effort and time for changeover are minimal.
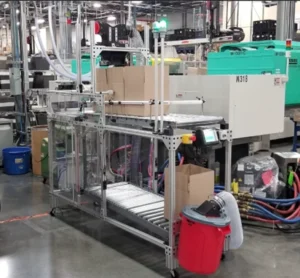
Hansen Plastics Corporation’s Innovation Is Up in the Air
Hansen Plastics was recognized for submitting a noteworthy labor solutions entry that appears in the 2023 MAPP Innovation Award Best Practice Book. The company implemented automation techniques that handle the output of two presses producing the same part.
The “before” – picture at Hansen for these two presses looked like this: Molded parts from each press fell into a chute and then into a plastic bin on the floor. An operator lifted the box to dump the contents onto an inspection table; good parts were moved to a finished goods box on a scale, with parts added until the weight met the required part count. An operator on each of the three shifts spent 50% of the shift tending to this process, for a total of 12 hours per day. The “after” picture at the company depicts a fresh approach that features several automation techniques. The result virtually has eliminated the 12 hours of operator time and attention.
This set-up produces internal water-valve parts, but the same automation techniques can be used for other molded items. Hansen’s Mark Hill, manufacturing engineer, gave insight into the design, production and implementation of these solutions. “The system we built is capable of working with any lightweight, durable part that can fit into a 4-inch blower hose,” Hill explained. “It is a very flexible system that we can use on other jobs when this valve job is not running.”
The presses for this job now can immediately identify molded valve parts that are rejects. “A funnel under the mold catches all the parts when they drop,” said Hill. “During a good cycle, the parts pass through the funnel and are blown via a LineVac into an overhead hopper. But if the press determines that the cycle has produced rejects, based on its own internal parameters, it will send a signal to route the bad parts into a ‘rejects’ bin next to the press.”
The LineVac uses blasts of air to move the good molded parts from both presses into a single overhead hopper system, and actuated doors in the hopper system drop parts into finished goods boxes. “The overhead hopper is all 3D printed,” Hill explained. “When the good parts are blown into the hopper, an area sensor detects that a ‘shot’ of parts has entered the hopper. A ‘shot’ is the full cavitation of parts the mold produces, usually four, eight or 16 parts. After the hopper has detected the parts, it waits until the air has stopped blowing and then opens the hopper doors, dropping parts into a finished goods box.”
The quantity of parts required to fill a finished goods box is a calculation that is monitored by the system as the “shots” of parts accumulate. “When the correct number of shots has been reached,” said Hill, “the system activates a conveyor and an elevator to shuttle the full box to the front of the system where the parts are inspected a final time and then packed onto a pallet of good parts.”
Hill described the biggest challenge in designing and configuring this system. “The most challenging aspect was the elevator itself,” he said. “Since this system design requires an ‘over-under’ style of box conveyor, it requires a finished goods box to seamlessly move from one elevation to another.” This requirement presented a conundrum at first; the elevator had to move a box around and not drop the box or spill the parts. “I had seen other systems use a large pneumatic slide to act as the platform,” Hill explained, “so I tried that out. After a few iterations, and some box dropping, we got a pneumatic slider to work very well and carry the box gently between the two elevations.”
With this automation in place, nearly anyone – but typically, a material handler – can unload and reload the system, which is done on average three times per day. The project was 100% designed and integrated in-house, using many components that were internally fabricated and/or 3D printed.
As in many automation integration projects, there was an “aha!” moment at Hansen Plastics; its moment of realization revolved around the use of the LineVac. “Our aha! moment came when we realized that a system like this could be used on many of the products that we produce,” said Hill. “If the part can fit into a four-inch air hose, it will work in this system.”
After determining that 30-40% of what Hansen produces could fit into that category, the company made sure that the system was designed to be as broadly applicable as possible. “No aspect of the system was designed to only cater to one specific part; it was designed to be truly universal automation. This system has been adapted in many ways to create other manual and automated stations, all of which help increase our labor efficiency and allow us to run more presses with the same number of people.” n
More information: www.falconplastics.com,
www.hansenplastics.com