By Andrew Carlsgaard, business relations manager/analytics director, MAPP
Based on feedback from 86 processing executives, MAPP’s 2023 Automation Report outlook for automation in the US plastics industry generally is positive, with increasing interest in adopting automation technologies to improve productivity, efficiency and competitiveness. Like many other manufacturing sectors, the plastics industry in the US has been embracing automation and robotics to address challenges such as labor costs, increasing international competition and demand for higher-quality plastic products. However, the pace and extent of automation adoption may vary by organization depending on factors such as the company’s size, the type of plastic manufacturing processes, and, most importantly, the available resources for investment in automation technologies. The primary factors shaping the outlook for automation in the US plastics industry include increased market demand for automation, cost savings and efficiency gains, improved quality and safety, skilled labor challenges and environmental sustainability.
With the growing need to enhance productivity, reduce labor costs and improve product quality, plastics manufacturers are increasingly adopting automation technologies. Advancements in robotics, machine learning and other automation technologies are driving the adoption of automated systems in the plastics industry. In MAPP’s 2023 State of the Plastics Industry Report, industry leaders identified investing in automation as the top competitive strategy for 2023 and plan to spend significant capital dollars to bolster this side of the business. Over 90% of the respondents to MAPP’s 2023 Automation Survey indicated that some level of automation already has been implemented for their primary machines. Rapid advancements in automation technologies, such as collaborative robots (cobots), machine vision and data analytics, enable more sophisticated and flexible automation solutions in the plastics industry – most of which currently are being deployed by MAPP members. In addition, these advancements are enhancing the capabilities of automated systems, making them more versatile, adaptable and user-friendly. (Chart 1.)
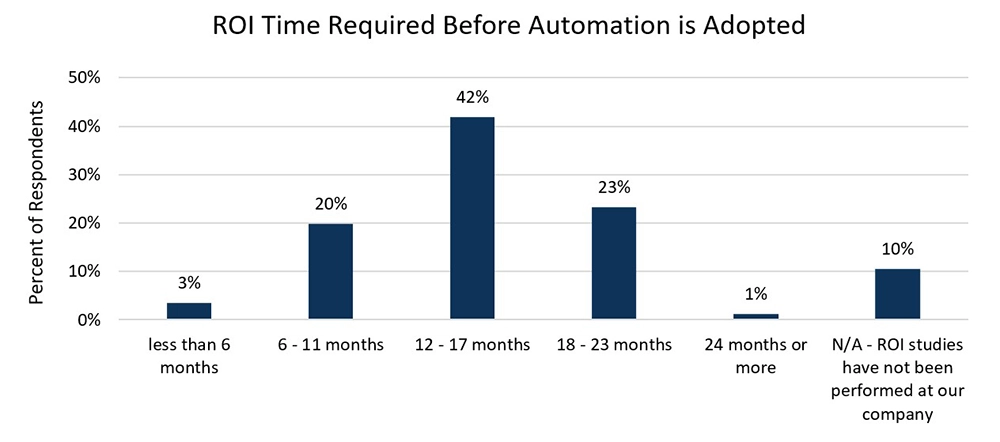
Automation can significantly reduce labor costs, minimize human errors and improve process efficiency in plastics manufacturing. Automated systems can operate 24/7, increasing overall production output and reducing production downtime, leading to cost savings and improved profitability for plastics manufacturers. In addition, it can help ensure consistent product quality by minimizing variations in production processes, reducing defects, and improving inspection accuracy. Automation also can help enhance workplace safety by replacing or minimizing high-risk tasks humans perform, reducing the risk of accidents and injuries. One Automation Survey respondent pointed out, “Sometimes ROI is achieved with employee safety – reducing our mod (EMR) rating.” Like many other industries, the plastics industry faces challenges in finding and retaining skilled labor. Automation can help mitigate this challenge by reducing the reliance on skilled labor and replacing repetitive and labor-intensive tasks with automated systems. For example, one respondent reported, “By automating and configuring our facility, we have eliminated the need for additional workers.” (Chart 2.)
Automation can contribute to environmental sustainability by optimizing material usage, reducing waste and improving energy efficiency. Highly automated systems can optimize production processes, minimize material waste and enable precise control over production parameters, leading to more sustainable manufacturing practices. Federal, state and local government mandates may be a significant driver for adoption at specific organizations, depending on their facilities’ locations.
However, it’s worth noting that adopting automation also has potential implications for employment, as automated systems may replace some jobs. Therefore, proper workforce planning, retraining and reskilling efforts may be required to ensure a smooth transition to an automated environment while addressing potential workforce challenges. Additionally, finding skilled automation labor in-house is increasingly difficult given the current shrinking of the talent pool in manufacturing generally, leading to potentially costly implementations using more third-party labor (most respondents preferred a hybrid approach).
Overall, the outlook for automation in the US plastics industry is positive, with leaders indicating an increased adoption (and interest in adoption) of automation technologies to drive productivity, efficiency, quality and sustainability. However, the pace and extent of automation adoption may vary depending on factors such as the company’s size, the nature (or market) of the plastic products being manufactured, and the availability of skilled labor, among others.
Nevertheless, collaboration and best practice sharing can help maximize the benefits of automation while addressing potential challenges. Best practice sharing through the MAPP Automation Initiative will help provide the resources member organizations need to build automation capabilities up to the best possible level known to the industry.
Further analysis is available by purchasing MAPP’s 2023 Automation Report through www.mappinc.com. To become a member of MAPP, email the MAPP staff at [email protected].