by Liz Stevens, writer, Plastics Business
Planning as far out as possible, having resin alternatives available for substitutions and being ready to jump on spot opportunities are good tactics, but the trio of experts had more advice for managing resin inventories, and for anticipating and planning how to weather future supply chain disruptions.
“Given the current tight resin inventory supply chain-wide,” said DELMIAWorks’ Louis Columbus, “real-time production and process monitoring become indispensable for identifying where resin is being wasted in the production process.” He described that the most common metric for measuring waste is the amount of scrap produced. Using real-time production and process monitoring, processors can do a root cause analysis to pinpoint where scrap is being generated, allowing for fixes to be implemented, which will save resin from being depleted unnecessarily during production. “Having sensors on resin feed machines and throughout each phase of the production process provides invaluable statistical process control (SPC) data to keep processes within operating boundaries that optimize the use of resin inventory,” Columbus said. “Building a real-time feedback system capable of providing a 360-degree view of how the resin is being consumed, transformed and shipped is vital to getting the most value from limited inventories today.”
Jenny Christensen, who represents not only Garner Industries but also BinMaster, a maker of resin silo sensors and developer of the ResinView® app, pointed to another way that resin monitoring can be an advantage during resin supply chain crunches. “Today, you can’t fly blind when it comes to inventory; you need 24/7 visibility and in real-time,” she said. “You are competing with other molders and manufacturers for resins that are in high demand, so you need to be out in front of it. With BinMaster sensors and ResinView® software, you can clearly see when the silo was filled and how much resin was used over time.” Christensen went on to explain that BinMaster sensors are always working to update inventory levels, so as resins are removed from silos, inventory levels are updated in just seconds. The sensors eliminate the need for climbing silos to measure the level, and they provide a dependable, current estimate of resin volume.
ResinView software displays not only the current level, but also tracks the level in the silo over time, offering a trend line for gauging how fast resin is being used and projecting when a silo will be empty. “Getting alerts is one of the most valuable ways an automated system can help,” Christensen said. “ResinView® tells you when you reach a low level by sending a text or email alert.” Since everyone in the plant has access to the same software and data, everyone is on the same page, allowing purchasing and production departments to work together to prevent, or at least be aware of, potential supply chain interruptions. ResinView® also allows users to place orders directly with suppliers, schedule deliveries and track the delivery dates per silo. Processors using multiple silos containing the same resin can see the entire inventory of each type of resin. They can use ResinView® to pull resin from another silo if one gets low or, for multiple locations, to see when it is time to move resin between plants to prevent shutdowns.
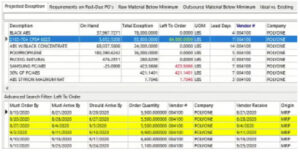
Columbus agreed with Christensen about the value of resin monitoring and tracking, noting that DELMIAWorks’ MES supports real-time process monitoring that captures data from programmable logical controller (PLC) based sensors like those offered by BinMaster. DELMIAWorks’ real-time process monitoring can capture, analyze and provide SPC and advanced quality analysis of the data the sensors generate. “Inventory monitoring and tracking provide the baseline of how much resin material a given processor’s production operation consumes in a typical shift for a given set of products,” said Columbus. “Knowing how slowly or quickly inventory levels fluctuate given a specific workflow of machines, operators and molds is a must-have for predicting future resin demand.”
Columbus described inventory monitoring and tracking as analogous to the speedometer and fuel gauge in a car. With a simple calculation of how much fuel is being burned at a specific speed, the driver knows how far the car can go before needing to fill up the tank. “It’s the same for processors,” said Columbus. “By monitoring and tracking data to know inventory and the speed at which it’s used for a given workflow and product set, they can get a very clear idea of how much they’re using – and that includes an allowance for scrap, setup and tear-down resin waste.” He also stressed that knowing how quickly or slowly a production line runs can help to determine how much resin a processor will use. “Due to all these factors,” he said, “the greater the accuracy of inventory monitoring and tracking, the more efficient a production line will be, and the higher the product quality. Without inventory monitoring and tracking, processors are flying blind, not knowing when they are about to run out of resins and will have to shut down the line.”
Bruce Flannery, with Amco Polymers, heartily advocated for sensors and resin inventory management tools: “We do have customers who have those sensors and software. I can actually log into some of our customers’ portals, see how much resin is in the silo and check on their production forecast for the next four weeks.” The resin supplier does not have access to any of these processors’ parts or customer data but can see the production forecast by pounds of consumption per day. With this insight, Amco can set up deliveries to customers’ silos. “They are not coming to us to book deliveries; we are actually going onto their portals, looking at what they have in their silo and how big the silo is, and then setting up the shipments as far in advance as possible.” The processors retain control of their inventories but by giving the resin supplier access to some of their data, Amco is in a much better position to predict and solve problems that may crop up long before the problems become acute.
Given the recent history of what unforeseen problems can hit the supply chain, Flannery believes that processors should adopt tools like silo sensors and inventory management tools. “Now is the time,” he said, “because everybody has been through supply chain disruption in one form or another lately, and the solution is really all about planning and being transparent with each other so that everybody can work together. I am for all of those things and some of the more advanced customers are using them already.”
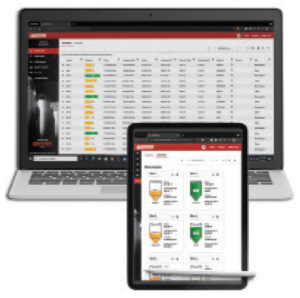
BinMaster’s ResinView® allows plastics processors to grant inventory access to their suppliers. “For example, processors can provide ‘view-only’ rights to their suppliers, so they also can monitor inventory proactively and project when the next order will be coming,” said Christensen. “This enables suppliers to have the right resins on hand when they are needed.” Christensen stated that allowing vendors to engage in the supply chain process leads to fewer rush orders, less overtime and a reduction in unexpected deliveries. “Vendor managed inventory can help build stronger relationships between processors and suppliers by letting them be part of the process,” she said.
ResinView® offers additional features for managing supply chain and inventory. “An example of this is the Trucks feature,” Christensen said. “A resin supplier and the delivery truck driver both need to know that the entire delivery will fit into a customer’s silo. Order too soon and the entire delivery won’t fit, creating a problem for processors to resolve. ResinView® calculates how many truckloads or the portion of a truckload that each silo has available to store resin.” The software also produces reports on past resin usage that can be charted on a trend line for analyzing use and planning deliveries. ResinView® accommodates API calls from third-party software for analysis of its data in other systems.
Columbus provided some insight into the aspects of DELMIAWorks’ software that address inventory management and the supply chain. “It’s best to visualize inventory monitoring and tracking as a real-time system that continually tracks inventory and outsourced parts throughout the manufacturing process to reduce physical inventory time and forecast the necessary materials to meet demands.” Plastics processors’ requirements are core to the company’s DNA; its founder invented DELMIAWorks while running a plastics processing plant. “We support separate inventory master records for each manufacturing individual location (or ‘EPlant’),” said Columbus, “both eKanban and conventional Kanban control support, and complete lot number tracking and traceability, including supporting documents. We’ve also delivered our DELMIAWorks manufacturing inventory management systems to meet manufacturers’ serialized inventory control requirements.”
Other tools included in the DELMIAWorks manufacturing inventory management system include vendor managed inventory capabilities, which support managing consignment inventory stored at customer or vendor sites; intercompany transactions allowing multi-plant companies to achieve unified scheduling and distribution across all facilities; shelf life management, which tracks expirations and automatically identifies non-conforming inventory with email alert notifications; and blend and formula technology that allows users to maintain items that are made up of two or more materials or ingredients.
“When processors have a real-time, integrated system that automates capturing, reporting and analyzing supply and inventory information as DELMIAWorks does,” said Columbus, “resin planning, purchasing and production are optimized for their specific plant operating constraints.” Columbus noted that with tools like these, for the first time, it is possible to adapt in real time to resin supply chain constraints, for example, or a change in customer demand without having to slow down to handle these processes manually. “Automating supply and inventory information for resin planning, purchasing and production are all about speed and how adaptive a processor can be – and that’s the best path to staying competitive.”
In an industry that now regularly throws curves to plastics manufacturers, it pays to be agile and adaptable, and to have the tools and resources to stay on top of resin levels on hand, resin availability and alternatives, and the state of the supply chain. Cultivating strong relationships with resin suppliers can give processors a real “heads up” about the next curve ball, and a partner with which to plan and respond quickly to minimize disruption to the supply chain and the production schedule.
More information: Amco Polymers, www.amcopolymers.com; BinMaster, www.binmaster.com or [email protected]; DELMIAWorks,
www.3ds.com/delmiaworks or 805.227.1122.