by Al Fosco, Marketing Manager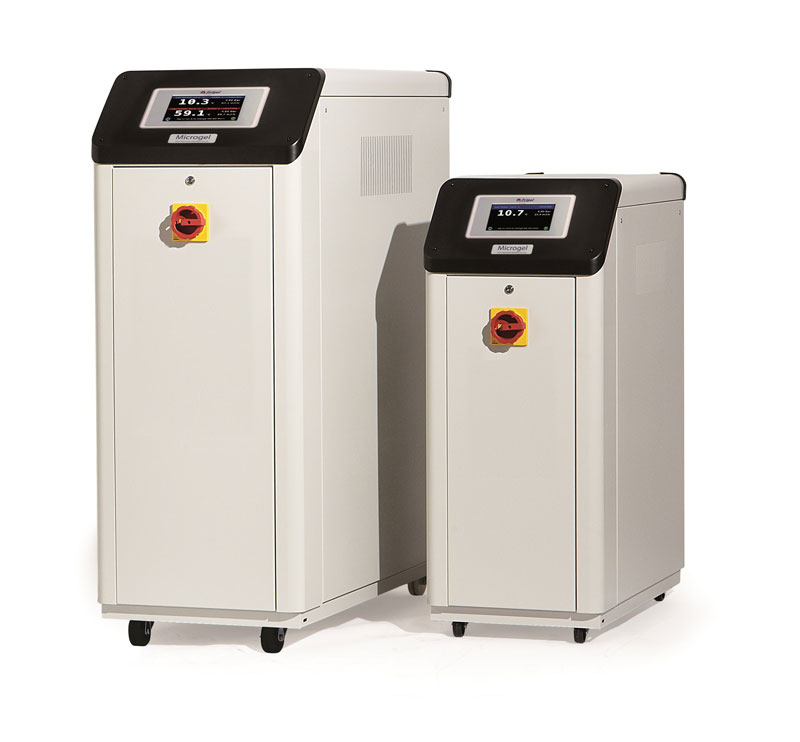
Frigel North America

Business-savvy plastics processors have long leveraged process cooling to gain a competitive advantage. And now, with readily available machine-side cooling data, processors can take it to the next level to further increase productivity and profitability – all while ensuring the ongoing delivery of quality products.
Machine-side cooling 101
The primary function of process cooling is to remove heat from whatever heat exchanger is used in the process, such as an injection or blow mold, chill roll or pipe/profile extrusion tank. Many processors have found the use of machine-side cooling to be an attractive alternative to traditional process cooling methods when it comes to a positive impact on the bottom line.
One traditional process cooling approach involves the use of an open cooling tower that delivers process-cooling water directly to the heat exchangers. Another involves a central chiller for the same purpose. The challenge with both is the inability to tightly control three main process-cooling parameters: coolant flow, coolant pressure and coolant temperature. As a result, opportunities for increased productivity and profitability can go wanting.
As an alternative, many processors have adopted the use of a closed-loop adiabatic central cooling system that provides cooling water to mobile, machine-side temperature control units (TCUs) or combination chiller/TCUs that are dedicated to a given machine or process. The approach gives processors the ability to optimize coolant flow, pressure and temperature to match the conditions of every heat exchanger to achieve optimal results.
Better data = better business decisions
The need for more data and the ability to make informed decisions related to process cooling has fueled the steady march toward more technically advanced machine-side cooling equipment. The advancements have largely taken the form of digital controls that processors can leverage to gain a higher level of control of coolant flows, pressures, temperatures and even energy consumption in process cooling.
Technically advanced machine-side units provide real-time data points for key cooling variables while serving up the information via user-friendly touchscreens. The controls also provide Wi-Fi connectivity for easy access to data even though machine-side cooling units are frequently moved from location to location within the plant.
Digital controls and the data provided give users the ability to easily set up, monitor and document what’s happening in all phases of cooling for each machine or process in real time – and make the necessary adjustments for a number of variables. In so doing, processors are better able to optimize the efficiencies and performance of the entire cooling process and the quality of the produced product. Importantly, data supports the need for repeatability for every production run from start to finish.
The value of data: a closer look
The use of digitally controlled machine-side cooling units in injection molding is a prime example of the value that readily available data delivers.
In injection molding, process cooling typically consumes 60 to 70% of a molding cycle. That means nothing else is happening in the molding process while the mold cools. Yet, with advanced digital controls, users can leverage historical data to more easily establish proper parameters and make necessary adjustments for coolant capacity, pressure and flows to reduce the amount of time needed to cool any given mold. The result is an exponential decrease in cycle times, an increase in production and reduced scrap – all of which contribute to improved profit margins.
Given that injection molders run operations with multiple machines, multiple molds and molds that each can have many different circuits that each require different flows and/or precise temperatures, it’s easy to see how digital controls and well-defined data set points can not only improve mold efficiency and performance, but overall efficiency of the operation.
With new, advanced digital controls, processors can say goodbye to spreadsheets and guesswork since data is at users’ fingertips. This new generation of digital controls tracks and displays all key process cooling parameters, including the following:
-
- cooling capacity used for mold validation, usually in tons or kW;
- coolant type (water or water/glycol mixture);
- coolant supply pressure to the mold, in psi or bar;
- flow rate (gpm or lpm) from the cooling system, as well as individual flows for each mold circuit; and
- coolant supply temperature to the tool, in °F or °C, as well as ΔT across the tool and each individual cooling circuit.
Some advanced machine-side units also give users process cooling energy consumption data over time, which is an important new development, since energy use for cooling is highest at the machine. Unlike before, processors now can measure the kW cost to cool each pound of plastic and cover it in the price of the final products for improved margins.
Processors also can add flow meters to machine-side cooling units to gain even more insights into flow data with a high level of accuracy. This results in the best possible mold performance based on the unique characteristics of a given mold, no matter how complex the geometries.
Digital controls on machine-side units also now provide troubleshooting features with accurate, real-time information and display it in easy-to-understand language to help users quickly resolve issues. Additionally, alarms and fault indicators help users identify issues and resolve them before they impact uptime and productivity. Some also offer remote monitoring capabilities to further aid in diagnoses and further increase uptime.
Informed decisions are better decisions
In an increasingly competitive environment where margins often are razor thin, virtually every decision matters. Fortunately, new generation machine-side process cooling units provide the data needed to more easily and accurately make informed decisions and gain tighter control of process cooling, resulting in operational efficiencies, increased profits and more opportunity for growth.
Al Fosco is the marketing manager for Frigel North America. Prior to joining Frigel in 2009, Fosco spent 16 years with Conair’s Water Products Division, holding sales and engineering management positions, including vice president of sales and marketing and general manager of engineering. Prior to that, he spent 14 years in engineering and sales management at AEC. He has a master’s degree in heat transfer and fluid mechanics engineering from the University of Illinois.
More information: 847.540.0160, a.fosco@frigel.com or www.frigel.com