Plastics Business
Additive manufacturing. Fused deposition modeling. Rapid prototyping. 3D printing. Whatever you call the process, additive manufacturing has undergone a perception change. While prototyping remains a key functionality served by additive manufacturing equipment, 3D printing is gaining acceptance as a method of short-run production.
Plastics Business interviewed Joe Hiemenz, technical communications and public relations manager for Stratasys, Inc., and Patrick Gannon, engineering manager for rp+m, to discuss their perceptions of the ways additive manufacturing is changing the face of the injection molding industry. Stratasys is a producer of additive manufacturing equipment and inventor of fused deposition modeling, and rp+m uses the technology to create prototypes, while also exploring additional uses, including short-run production.
How is additive manufacturing used today?
Both Hiemenz and Gannon agree that additive manufacturing is used in two primary ways: rapid prototyping and direct digital manufacturing in low volume. “For prototyping,” Hiemenz explained, “there are two areas in which additive manufacturing is used: concept modeling and functional prototype testing. For direct digital manufacturing, there also are two areas: fabricating manufacturing tools (like jigs and fixtures) and for the low volume production of finished goods.”
Stratasys has noted the use of additive manufacturing for prototyping in almost every industry by design engineers who want to prove out the design before going to production. These industries include aerospace, automotive, defense, education, medical, consumer product industries and business and industrial machinery.
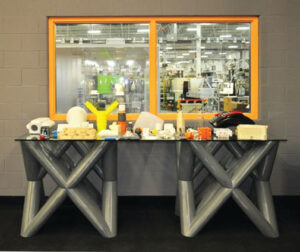
At rp+m, the company operates as a service bureau, supporting the production and engineering sides of sister company Thogus Products Company, an injection molder, with assembly fixtures, design builds and prototyping. rp+m also has customers for which it prototypes and produces short manufacturing runs.
“I wouldn’t say prototyping and manufacturing are an equal mix,” said Gannon. “Volume leans more to the prototype side, and it’s still the use people are most familiar with, but I’ve seen an uptick in quoting for manufacturing for final product.” Gannon stated that rp+m is making an effort to spread the word about its manufacturing capabilities, particularly for customers who need a smaller production run.
What are the limits of additive manufacturing?
While gaining in popularity due to its ability to manipulate materials in ways not possible with traditional injection molding, additive manufacturing isn’t the answer for every situation. As Gannon mentioned, the costs associated with additive manufacturing often eliminate certain types of production runs. “It’s tough, because you’re not going to compete on piece price with an injection molded part on larger runs,” Gannon explained. “There’s a moving line for where it makes more sense to do additive manufacturing or when injection molding is the best choice, and it often depends on the type of part and the type of resin needed.”
Resin remains a severe limit for the additive manufacturing process. The equipment manufacturers often limit the types of resins approved for use, which subsequently limits the type of products that can be produced. “Thogus has 200 active materials for injection molding,” Gannon said. “At rp+m, we have ten active resins. We’re doing some research, along with our polymer representatives, to run different resins through the machines, and we’ve been somewhat successful, but we’ll never have the material range that is available in injection molding.”
How is additive manufacturing impacting plastics processing right now?
Stratasys has seen an increase in the number of plastics processors adopting additive manufacturing, putting it to use in strategic ways. “Molders are using the equipment to make a model of the part during the quoting process,” Hiemenz stated. “They can deliver the model, along with the tooling and production quote, to the customer, and at the same time make recommendations for a design change if it could improve product performance or reduce the tooling or production cost.”
Gannon seconded the value of having an actual model in hand when discussing production with customers. “You can always do something on the screen,” he said, “but for most people, holding it in their hand and pointing to things is how they actually get it.”
Gannon went on to say that he has seen a number of processors starting to catch on to the possibilities of additive manufacturing. “They see that they can provide this value to their customers very easily, and in some cases, very cheaply,” explained Gannon. “That’s what happened to us. Our first machine was bought specifically for injection molding, so that we could print the customer’s part and send it back to them.” Then, Gannon said, innovation took over. “Once the equipment was in-house, and we had a bunch of engineers standing around it, there was no more ‘water cooler’ conversation,” he laughed. “Now it’s 3D printer conversations! You put two engineers in a room with a 3D printer, and they’re going to think of 10 things to do with it.”
What trends have been identified by Stratasys?
One of the trends Stratasys has seen is that molders aren’t limiting additive manufacturing to prototyping. “Of this group of users, some use it for 5S operations, creating tool boards that aid organization by having a designated home for each tool,” said Hiemenz. “Still another way we’re seeing molders using additive manufacturing is to build custom robotic end effectors to pick and place injection molded parts. When users get their hands on additive manufacturing equipment, innovation naturally occurs.”
Hiemenz sees the pace of additive manufacturing adoption increasing in 2012. “When these manufacturers see how additive manufacturing can lead to more business or reduce costs, the purchase becomes easy to justify,” he explained. “The word is getting out and awareness is going up. It’s not just the forward-looking companies adopting additive manufacturing; more and more, it’s becoming a mainstream tool.”
How will rp+m push the limits of additive manufacturing in 2012?
rp+m has a full range of Stratasys 3D printing equipment, including two Fortus 400mcs, two Dimensions, a uPrint desktop 3D printer, a Fortus Finishing Touch Smoothing Station (to vapor-smooth and seal the parts) and a Fortus 900mc, which can make parts up to 3 feet by 2 feet by 3 feet. With this variety of additive manufacturing equipment and two engineers dedicated to the process, rp+m is stretching the limits of the technology.
“We have a great process that makes strong parts, but one of the limitations is the durometer of the material,” Gannon said. “Some of the other presses can make soft parts, so we’re working on end of arm tools that have soft touch materials on the contact points. We’re trying to place in-mold labels with a 3D printed, soft touch part with a vacuum line in it.”
rp+m also continues to build the resin variety available for its additive manufacturing equipment, which would expand the production possibilities. “Once you start thinking of new ways to use the equipment, you never have enough capacity,” Gannon explained. “Additive manufacturing gives us a limitless ability to design.”
For more information, visit www.rpplusm.com and www.stratasys.com.