by Dianna Brodine, managing editor
Plastics Business
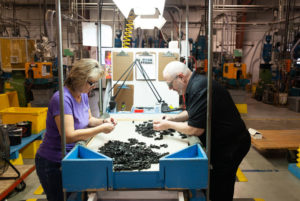
Fighting global competition requires resources that may be beyond the reach of small- to midsize manufacturing companies. As far back as 1962, the US government attempted to level the playing field with the Trade Adjustment Assistance for Firms (TAAF) program.
According to a 2017 Congressional Research Report, “The Trade Adjustment Assistance (TAA) programs were first authorized by Congress in the Trade Expansion Act of 1962 to help workers and firms adapt to import competition and dislocation caused by trade liberalization… TAAF provides technical assistance to help trade-impacted firms make strategic adjustments to improve their global competitiveness.”
Eleven TAAF centers across the US work with manufacturing companies to develop and implement projects that strengthen their organizations and increase their competitiveness. But, many plastics processors have never heard of it – and the Great Lakes Trade Adjustment Assistance Center (GLTAAC) wants that to change.
Matching funds for development through TAAF
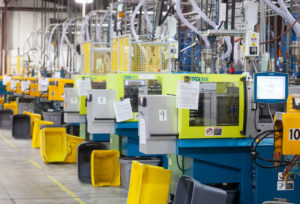
“We’re one of 11 centers around the country, and we manage the Michigan-Ohio-Indiana region,” said Scott Phillips, senior project manager for GLTAAC. “We are part of the Economic Growth Institute at the University of Michigan, and we’re funded by the US Department of Commerce.”
As Phillips explained, the TAAF program has been around since the early 1970s, but its reach has always been small. “We typically work with one to two dozen new companies a year,” he said, “and across the US, all the centers together usually are working with 500 to 600 companies in total.”
Nationally, the program is funded in an amount that has ranged from $12 million to $16 million per year. The program is open to all types of companies, and though almost all are in manufacturing, the predominant type of manufacturing served by the TAAF centers varies based on location. “The centers are structured so that the companies accepted into the program can get the specific type of assistance that is needed,” explained Phillips. “In our area, we work with mold makers, plastics processors, and tool and die manufacturers. In the northwest, the center may work with more salmon fishers or in Texas, it could be small food processors.”
Phillips, whose job is focused on outreach, works to find companies that fit the program and can meet three criteria for qualification, based on level of sales, level of employment and the degree to which imports have impacted the company. First, sales must be down 5% over a recent period of time. Second, employment head count must be down 5% over the same period of time. Finally, evidence must be presented that shows the impact of competitive imports. “Typically, that means the company must show that the purchase volume of at least four customers is down,” Phillips explained. “We need to speak to two of them, and at least one of them must validate the fact that purchases are down because they’ve been resourced to an offshore company.
“In a five-minute phone call, we can almost always figure out if a company is eligible because the criteria are pretty straightforward,” he continued.
Once the company has taken the first steps toward qualification, GLTAAC submits a petition on its behalf for review in Washington, DC. GLTAAC also makes a site visit to talk with the client and perform an assessment of the business.
“We work with the company to decide on the best way to use $150,000 over five years,” explained Phillips. “Half of that – $75,000 – is a grant from the program to match $75,000 in funds from the company.”
Helping manufacturers compete
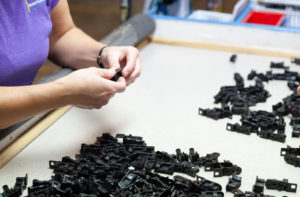
TAAF is designed to meet the needs of the manufacturer, so its funding parameters are fairly broad. “If you’re a small company and all of a sudden you’re confronted with additional foreign competition, you probably don’t have the internal capabilities to deal with it,” said Phillips. “The program allows manufacturers to bring in outside service providers to build their capabilities and competitiveness.”
Examples of projects to be undertaken could include sales lead generation, market research aimed at diversification into new markets, productivity improvements, ERP or MES implementation, management training, succession planning and more. Capital expenditures are one limitation – equipment and building additions cannot be funded.
GLTAAC staff help companies assess where best to focus their efforts. “When we go in to create a spending plan, we begin with a site assessment,” said Paul Crossley, senior project manager. “We look at all functional areas: management, sales and marketing, financial, production and support services, such as human resources and information technology.”
The assessment includes interviews with company leadership to help form a high-level picture. As the plan develops, follow-up calls with department heads and other staff members occur to help GLTAAC dig deep into what the company is doing and where the opportunities are for improvement.
“Part of what we do is help companies figure out what they need to do, what they have the internal capabilities to do and where they need outside help,” said Phillips.
Crossley added, “Our function is to come in and help them define what is needed. We’ll make recommendations based on what we see, but ultimately the company decides what they want to do. Our function is to provide information based on our experience.”
Once a plan is finalized, it must be submitted for approval. Then implementation mode begins. The program allows five years to identify the scope of work, chose an outside solution provider and create a three-way contract between the solution provider, TAAF and the client. Before the contract can be finalized, parameters for the outside provider must be met, including proof of outside expertise, a set project duration and the definition of clear deliverables.
As the project progresses, the plan is able to adjust. “We are working with distressed companies,” said Phillips. “A plan that is developed today may not be perfectly meaningful and useful a year later. We have up to two years to redesign the plan as the company’s needs change.”
Bamar Plastics benefits from TAAF
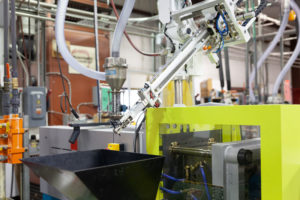
Bamar Plastics is a precision custom injection molder located in South Bend, Indiana. Family-owned since 1978, Bamar learned about the TAAF program during a chance meeting while exhibiting at a tradeshow.
“When I came on staff five years ago, this company was in the red,” said Heather Meixel, CEO and president. “Bamar had lost a ton of its original business to China, and we were hurting.”
Bamar had always exhibited at the Buy Indiana Expo, and one of the people who stopped by the booth was a longtime member of the injection molding industry. He introduced Meixel to the program, and she immediately saw the possibilities – even though she was a little surprised it wasn’t more well known. “The program has been around for over 30 years,” Meixel said. “I grew up in this industry, and I’ve never heard of it.”
Once qualified for the program, Bamar chose to focus on four projects: a website update, an IATF compliance program, lead generation and IT infrastructure.
“We worked for a few months to get through the initial introductions, and then we had to find the things that would add value to us,” said Meixel. “After that, we had to establish a scope of work for these different outside companies. That forced my management team to sit down and figure out exactly who was going to do the work for us and how they were going to do it. We had to decide on measurables and communicate what we were trying to get out of this. I can’t tell you the domino effect of benefits that happen when people start talking about the scope of a project in a way that helps them understand the goal.”
When working with the TAAF program, the manufacturing company is able to choose its own outside vendors. “The most important part is the cultural fit between the company and the consultant,” said Phillips. “Some companies already know a consultant and have a prior relationship. However, some companies don’t have that knowledge or previous relationship, so we can provide three or four potential providers if needed.”
Crossley added, “There’s a due diligence process, and our function is to oversee that, but we’ll defer to the company unless we see a mismatch.”
Once the scope of work had been finalized and the consultants identified, the project implementation began.
“Bamar was in a position where the company could accept more business,” said Crossley. “My focus was on helping them with lead generation. We began with a prospecting firm that would go in and meet the prospective client, understand their needs and really do a lot of the leg work associated with drumming up business. We also had an IT firm come in and help them with some of the day-to-day IT management issues.”
The site assessment process gave Meixel and her team time to think about what processes were effective uses of their time. “Just like payroll, IT is a service that can be offloaded,” she said. “I wish we had done it sooner. And now, everything we can subcontract, we subcontract.”
Meixel also hired a woman-owned start-up to redesign Bamar’s website. “The program is designed as a dollar-for-dollar cost share for services – bringing in services we probably wouldn’t have spent money on,” she said. “It not only helped with Bamar’s visibility and marketing, it helped further my goal of helping local small businesses. It helped me plug into things that are important to me, like hiring start-ups in our community.”
By freeing up resources and bringing in outside expertise, the TAAF program works to give manufacturers an advantage by letting them focus on the daily work. Crossley commented, “There are only so many hours in a day, and these small companies need boots on the ground. GLTAAC helps these companies on many levels in a strategic way, but we also help them with outside resources to give their management team the time to do the strategic work.”
GLTAAC tracks data to show that the work it does is impactful and helps companies stay in business. “We have a 97% five-year survival rate,” said Phillips. “We track sales and employment – our companies typically have significant sales and employment growth while in the program and after.”
Meixel has seen the results at Bamar Plastics. “We’ve brought on two new customers directly because of our involvement with the program,” she said. “For us, that’s huge.”
“There are no downsides to this program,” she continued, “and that’s very unusual for me to say! I’m not easily sold. But this program is painless, and I don’t know why anyone wouldn’t be interested in it.”