By Andres Abreu, business development manager, Packaging,
Branson Welding and Assembly at Emerson
An international effort to transition away from single-use plastic packaging and products in favor of sustainable, bio-based or recyclable plastics is underway. The goal is to reduce plastics pollution by eventually phasing out certain single-use plastic items, while developing a policy framework to improve the understanding, use and recycling of bio-based plastics (BBP) and biodegradable and compostable plastics (BDCP).
A major step in the effort is educating customers about what bio-based and biodegradable/compostable plastics really are. They exhibit a wide array of differences. For example, any plastic that uses 20% or more of biological feedstock is considered BBP, but without requirements to explain their other content, some BBP are biodegradable while others are not. In the same way, all BDCP are biodegradable, but there is no indication whether industrial composting is required, whether the material should break down in soil or water, or how long biodegradation should take. Initiatives are underway to provide answers and clarification surrounding these issues.
One US initiative involves some state legislators pursuing Extended Producer Responsibility (EPR) programs that require manufacturers to take greater life-cycle responsibility for the products and packaging they offer. In addition to demanding greater assurance that their products can be reused, recycled, composted or biodegraded, EPR bills aim to:
- Maximize recycling and collection potential
- Minimize the use of single-use packaging and plastics
- Increase manufacturer participation in “producer responsibility organizations”
- Increase beverage bottle recycling and recycled content in plastic products
At present, more than 250 manufacturers, which produce about 20% of all plastic packaging worldwide, are committed to having 100% of their plastic packaging reusable, recyclable or compostable by 2025. The list includes such major global corporations as Johnson & Johnson, Colgate-Palmolive, Unilever, SC Johnson, Mars, Apple, Nestle, Walmart, Coca-Cola, PepsiCo and many more.
One encouraging sign is how everyone in the plastics packaging value chain – resin producers, package and film producers, manufacturers/brands and technology suppliers – is pursuing new and effective sustainable package solutions that use BBP and BDCP.
As a leader in providing plastics packaging technology for bags, pouches, clamshells, cartons, coffee canisters, caps, filters, seals and more, Emerson is responding to the shift away from traditional plastics by evolving its plastics joining technology. Emerson is working with resin makers and packaging manufacturers to develop new joining profiles that will provide commercial-grade performance (now offered using traditional materials) for new and rapidly changing BBP.
It is a significant processing challenge, as newer bio-based plastics contain less polymer and process at lower temperatures with a narrower processing window. The differences between the temperature at which bio-based plastics melt and seal effectively and that at which they begin to degrade and lose strength are much smaller. Producing commercial-grade packaging and sealing at with such narrow margins for error demands a greater degree of temperature and process control.
In light of such strict requirements, manufacturers are questioning whether traditional thermal sealing equipment can provide the control and consistent, repeatable quality they need. Traditional heat-sealing methods compress opposing plastic layers between heated bars that must be controlled for temperature, pressure and dwell time to achieve repeatable quality. Unfortunately, BBP, with its narrower processing windows and heat sensitivity, make it nearly impossible for producers to hit the “sweet spot” consistently for repeatable package strength and performance with traditional thermal seals.
To meet the challenge of joining bio-based plastics, more and more packaging manufacturers are considering ultrasonic plastic welding, a far more sensitive, responsive, controlled process that uses heat to create the seal in a much different way. Traditional heat sealers surround the component parts with heat from the outside, using heated bars to compress heat through the plastic layers to the seal interface. Ultrasonic welders, on the other hand, create frictional heat within the plastic-to-plastic interface through high-frequency vibration. It is an “inside out” melt process that focuses heat only at the seal interface during the weld cycle (< 1 sec). It is an instantaneous process that also provides energy savings of 25% to 75%, compared to thermal sealing equipment, because it consumes energy only during each brief weld cycle. Thermal sealing methods consume energy continuously to maintain surface temperature of the heating bar, whether they are sealing or not.
Ultrasonic welding technology also provides for multiple modes of digital, closed-loop control, with process data collection, enabling precise control of every weld input and quality parameter. Energy input is controlled to the joule, downforce to the newton. In addition, with ultrasonic weld tooling resonating at an exact frequency (in Hz), it is possible to make micron-scale adjustments in amplitude to digitally fine-tune the heat generated at the seal interface. Users of ultrasonics can also monitor process parameters in real time, set high/low limits on weld results, and configure alarms that automatically identify weld cycles that are out of spec, enabling automated bad-part processing and data logging.
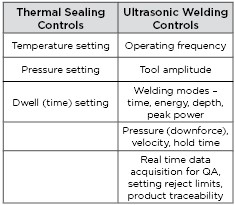
The fact is, manufacturers and packagers worldwide are answering the challenges of adopting bio-based plastic materials by implementing ultrasonic welding technologies that facilitate innovative products made with bio-based plastic materials. From compostable coffee pods to standup pouches and bags to sustainable food packages that use ever-increasing percentages of recyclable or compostable content, the market for bio-based plastic packaging is rapidly expanding.
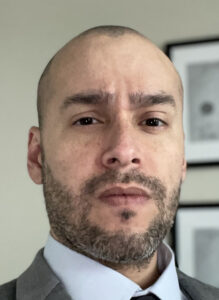
Andres Abreu is the business development manager, Packaging, Branson Welding and Assembly at Emerson. Abreu is a trends expert in manufacturing processes, government regulations and plastics materials. He holds a BS in electronic engineering from the University of Akron.
Enabling BBP in familiar applications
As governments struggle to sort out the complexities of reducing waste streams and boosting circular plastics use, the market for bio-based and recycled plastic packages is growing rapidly worldwide. Many of these applications focus on replacing petroleum-based plastics in popular, single-use products including:
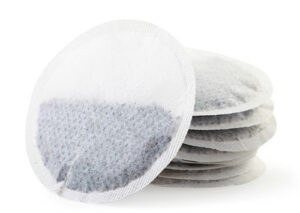
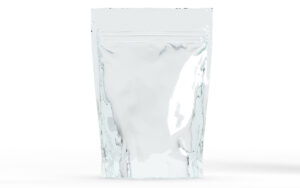
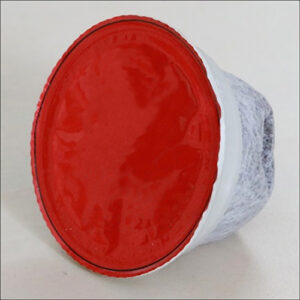
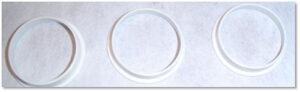
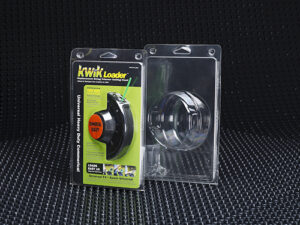