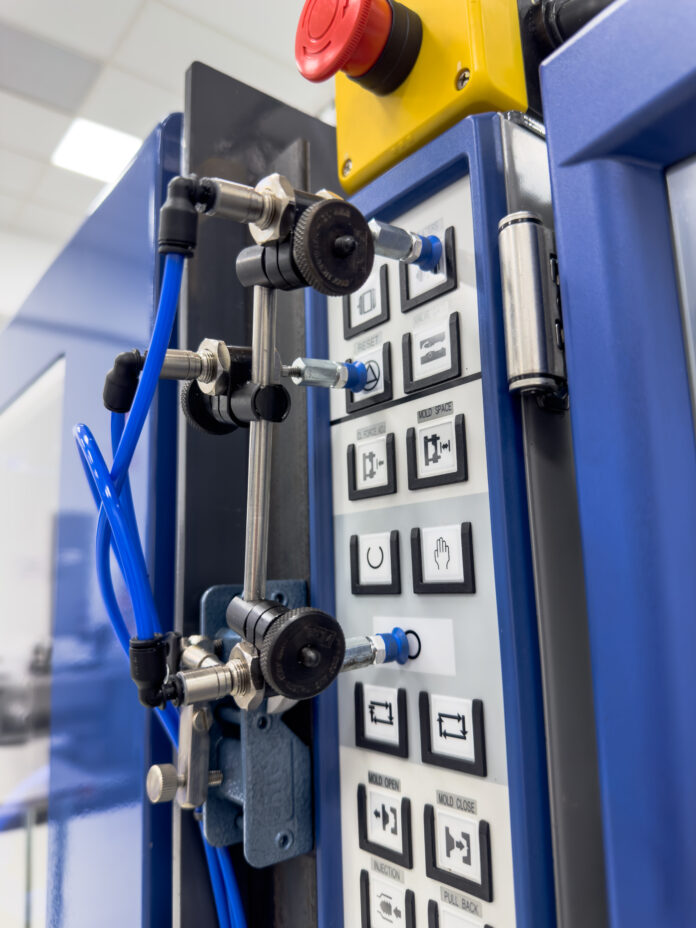
By Liz Stevens, writer, Plastics Business
What if? Outside-of-the-box thinkers use a “what if?” mentality to tackle plant operation challenges. Plastics processors are an innovative bunch and it’s a good thing. Keeping a multi-service or multi-line injection molding operation humming along – with its varied work cells, machinery, processes and tasks – takes skill and experience and, sometimes, a little something more. When challenges crop up, an outside-of-the-box mindset may be just what is needed to solve a thorny problem. Plastics Business found an exploratory frame of mind at two companies that recently earned MAPP Innovation Awards and took a closer look.
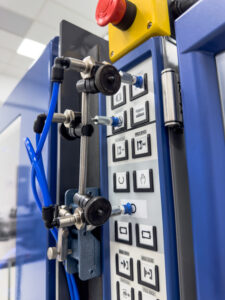
A New Twist on Machine Monitoring and Kicking Off Production Processes: Beaumont Advanced Processing
What if a company imagined the cells of its production operation as buildings on a piece of property and used a home security system to monitor the machines and to remotely kick off production re-start steps?
Beaumont Advanced Processing, Erie, Pennsylvania, provides a variety of services to the industry, including material characterization, production molding, test specimen molding, tool design, tool build, mold sampling and consulting. The company earned first place in the Smart Manufacturing category of the 2023 MAPP Innovation Awards for implementing and adapting home security technology to monitor and control plant machinery during overnight and weekend operations.
Beaumont Advanced Processing had a production volume that called for 24/7 and weekend operation, but the volume did not warrant a third shift or a weekend workforce. The main concern for night-shift and weekend processing was responding to issues that stopped the presses or turned off the secondary functions. Even though resolving an issue that caused a shutdown often required only a short amount of hands-on time, bringing a press back online required lengthy production startup procedures, such as getting the heat back up to operating temperature.
The company has found a way to alert processors via their cell phones that a press has alarmed, and subsequently expanded that approach to allow processors to remotely reset alarms and control secondary functions. By using a home security system and imagining each press work cell as a “building” on a “property,” the company takes advantage of the security system’s sensors to detect that a press has alarmed; and it even uses the security system’s ability to send electrical signals back to the “building” to reset the press alarm and restart the heating equipment.
Eric Bowersox, director at Beaumont, explained more of the details of the unique approach. “When a press alarms,” said Bowersox, “a signal sent from the PLC of the press prompts the home security system to notify the processors via their cell phones. They receive notification that there was activity at a certain location.” This is akin to a security app alerting someone to activity taking place on their property. The app, for example, can notify a user that there is an activity in the tool shed. “In our case,” Bowersox explained, “we saw that we could name our work cells by using the press name or number. When an alarm occurs, processors receive a notification that there is activity, for example, at Press #11. When they click on the notification, the app displays whether the press itself is alarming or whether the alert is due to something at the dryer, at the temperative control unit or a moisture sensor.”
Bowersox explained that a press alarm can be the result of any abnormality in the process conditions, from fill time to transfer pressure, cushion or screw recovery time, issues during mold close or ejection, or overall cycle time variations. He said that tapping a home security system’s built-in notification option is an economical and practical way to receive operational alerts. Organizing the work cells to be perceived as “buildings” on a “property,” however, took some creativity and configuring.
The company then tapped the home security system to go beyond alerting processors to problems or situations in a work cell. In instances of a press alarming because of an event that would shut down its associated heating equipment, Beaumont devised a way to have the home security app reset the press and even turn the heating equipment back on. “The app is designed to be able to turn on a light on someone’s property or inside their house,” said Bowersox. “We took advantage of that ability to send a signal back to the ‘property.’” Rather than having the signal sent to a light that is plugged into a smart plug, Beaumont’s app sends the signal to a control box that the company designed and built. The control box is connected to a set of mini pneumatic cylinders that are positioned at the controls of a press.
“Sending a combination of signals,” Bowersox said, “causes the pneumatic cylinders to push the buttons on the press controller to, for example, reset the alarm or power on/off the press heats. The home security system doesn’t know what is being turned on; it just sends a signal to release power.”
Bowersox explained how the combination of a home security system and custom control box can expand on what machine monitoring might deliver. “Much of what we are doing,” he said, “is not outside the realm of traditional machine monitoring technologies, but I do not think many, if any, machine monitoring systems allow a user to remotely clear an alarm and reset the heats.” He conceded that this may be possible with machine monitoring, but that Beaumont did not investigate this route due to the high price of machine monitoring systems vs. the economy of using a home security system with internally built add-ons. Bowersox also was pleased with the cybersecurity aspects of a home security system. “This is one of the benefits of utilizing a commercial security product,” he said. “They have a much better ability to handle cybersecurity issues than we do as a small, privately owned company. The system itself is monitored for hacking through the security company, while we control who has the credentials to log into the system and make any changes.”
In addition to remotely turning off an alarm or kickstarting a pre-production heating routine, Beaumont Advanced Processing is using the home security features to monitor other aspects of plant operation to catch problems as they emerge. “We are monitoring press-side dryers,” said Bowersox, “as well as temperature control units and moisture sensors. We have tied in cameras at the presses so that if the processors receive a notification from a moisture sensor, they can access the camera for that press and determine if it is a major leak or just a dripping hose or connection.”
Other applications apply to the overall facility, such as moisture sensors placed in the main facility that alarm if the septic lift pump is not actuating or if the septic tank is reaching max capacity. “We have found multiple opportunities to monitor in the main pump room where we have our chiller and tower water systems,” said Bowersox. “We also have tapped this system for use on the main air compressor that feeds our entire building.”
While this novel use of a home security system has been a major achievement, Beaumont won’t be content now to rest on its laurels. “We continually will keep an eye out for new opportunities to utilize this system,” said Bowersox. “Our company was founded on R&D in the injection molding industry; this kind of exploration always will be a part of who we are.” Beaumont currently is reviewing the steps for developing the best methods for molding machine process development. “We may find that nothing there needs to change,” Bowersox said, “but we always are going to dig into the status quo and see if we can improve.”
What if a company could tap the USB port of an injection molding machine’s IMM – normally used to output merely snapshots of operational data to a flash drive – and allow the molding machine to stream all of its data, continuously, for routing to the company’s IoT cloud service?
Noble Plastics, Grand Coteau, Louisiana, is an injection molding manufacturer that can produce in quantities from small-run prototyping to large-scale production on presses ranging from 35-940 tons. The core of the company’s services includes injection molding manufacturing, development of advanced automation and Industry 4.0. Noble Plastics was awarded the third-place award in the Smart Manufacturing category of the 2023 MAPP Innovation Awards for creating an economical, inventive hack to tap into IMMs to log huge streams of real-time data.
Noble Plastics sought to monitor the production data from its injection molding machines but found that older IMMs often lack the data servers necessary for this kind of data capture and storage. Retrofitting older machines to add data servers is expensive, if not impossible, and new machines may or may not have this technology. IMMs commonly do, however, have a USB port for downloading a limited-time slice of production log data to a flash drive. The company’s Scott Rogers described how Noble Plastics hatched a new idea for capturing real-time continuous logging of its IMM data.
“We often use the protocol function in our Arburg and Engel machines,” said Rogers, “to log process information over time to assess process stability and statistically establish parameter limits. This requires collecting data in batched format on a USB flash drive and moving the flash drive to a computer for analysis.” Rogers saw that almost every computer, whatever the size, also has a USB port. Instead of walking USB flash drives with small slices of production data from injection molding machine to computer, the company innovated by substituting single-board computers for the typical flash drives and by entirely eliminating the “walking” part of the delivery.
Noble Plastics pioneered the use of single-board computers (SBCs) plugged permanently into IMMs to continuously capture process data, and tapped the SBCs’ computing and communications power to deliver the data to the company’s cloud-based storage service. “This interface allows us to stream data to our established collection and analysis systems without any modification to the injection molding machine,” Rogers explained. “I built the first device before bringing it to our team for further collaboration and testing.”
Noble Plastics’ Jordan Price and Greg DeCuir described additional details of the company’s SBC-IMM innovation. A single-board computer is tiny – hold-in-your-hand sized. The single-board computer emulates a USB flash drive. Any log files that the IMM normally would write to a USB flash drive instead are directly written to the SBC.
Once the IMM writes a new log file to the SBC, the data within that file is made available through an OPC-UA server which is running on the single-board computer. A Kepware server acts as an OPC-UA client and remotely reads the data from the SBC and many other devices on the floor. The data from the SBC, along with data from other devices in the facility, is made available to process analytics systems, such as those offered by DELMIAWorks, Oracle or others, for analysis. The SBC uses ethernet for maximum communications reliability.
The type and volume of process data captured varies per IMM and according to what the company wants to monitor and analyze. For this project. Price and DeCuir selected 16 different parameters to export via the IMMs’ built-in logging tools.
Single-board computers are inexpensive and plentiful. Price and DeCuir have used Raspberry Pi, Beagle Bone and other industrial SBCs. The Raspberry Pi and Beagle Bone SBCs are in the $50 to $100 price range. A caveat is that some SBCs are designed for hobby use while others are made for industrial use. In general, SBCs offer good reliability and can operate continuously for extremely long periods. Most SBCs are solid-state devices and – another caveat – they can overheat, if not given enough airflow and perhaps a
heat sink.
For Noble Plastics, always on the cutting edge of technology, the challenges of incorporating the SBC innovation were minimal. One challenge DeCuir and Price faced was getting the injection molding machines to recognize the SBCs as attached storage devices. After that issue was resolved, enabling most of the additional functionality was straightforward. The biggest challenge after that was increasing reliability and uptime.
Noble Plastics has 20 USB-capable injection molding machines. Equipping each one with the technology to manage and transmit data to the cloud would have cost between $3,000 and $7,000, for a plant total of $60,000 to $140,000. A single-board computer, on the other hand, is in the $50 to $100 range, a tiny fraction of the cost to retrofit or upgrade an IMM. For Noble Plastics, the return on investment for single-board computers has been enormous.
As Noble Plastics and Beaumont Advanced Processing have shown, employing a healthy “what if” mentality can help plastics processors put the “smart” into their smart manufacturing. n
More information: www.bapmolding.com,
www.nobleplastics.com