“Alright stop, collaborate and listen …,” boomed through the speakers and Vanilla Ice’s hit song became the entrance music for 650 manufacturing professionals to the Indianapolis Downtown Marriott’s main ballroom, kicking off the Benchmarking and Best Practices Conference. The conference was held October 2-4 and, over those three days, attendees took advantage of connecting with like-minded professionals, forged partnerships with leading solution providers and gained a competitive edge through roundtable discussions delivering practical strategies, real-world case studies and actionable insights.
The Manufacturers Association for Plastics Processors presented a theme for this year’s conference, “Ingenuity at Work,” reflecting its commitment to innovation, engagement and forward-thinking solutions.
With “ingenuity” at the forefront, Troy Nix, MAPP executive director, appeared on the stage to set the tone and said, “Getting unstuck can be challenging.” He continued that being stuck is part of the journey and it happens to everyone, but changing a few daily habits can create a new path – leading to becoming “unstuck.” While there’s no right or wrong way to get “unstuck,” here are three habits that he encouraged:
- Find the beauty (in being stuck, teammates, daily tasks, small victories, etc.).
- Change how you speak to yourself. It’s a mindset. Be compassionate.
- Just start moving. It’s progress, not perfection.
“You don’t have to have it all figured out to move forward,” said Nix. Attending the Benchmarking and Best Practices Conference, whether an industry veteran or young professional, is a step toward a better tomorrow and getting unstuck – creating change and putting “ingenuity” to work.
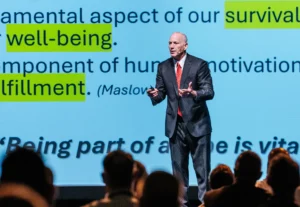
“Blow the dust off!”
Known as the master of ceremonies for the Benchmarking and Best Practices Conference, Nix walked on the stage with confidence but – unbeknownst to his audience – he was about to get uncomfortable and tell his story about “the power of belonging.” He said, “What is one thing you refuse to do because the thought of doing it makes you so uncomfortable?”
For the next 15 minutes, Nix told his story about shattering comfort zones, putting forth the effort and the “why” behind choosing to face his fears and take on the challenge. Where did it start? At the 2023 Benchmarking Conference, Nix encouraged attendees to get out of their comfort zones, and 10 days following the event, he seized the opportunity to get out of his safe space and began training in jiu-jitsu. Nix’s goal was simple – to shatter his comfort zone with the following objectives:
- Physical challenge – pain from the activity.
- Mental challenge – hard to learn under pressure.
- Grow and develop – changing the mindset; measure success in how many failed attempts; and keep showing up.
- Create relationships with driven purpose – hardest objective = fit in; everyone just wants to fit in.
Over the past 51 weeks of the jiu-jitsu program, Nix said he, “… put forth the effort to belong.” In that time, he had to persevere, meet challenges head-on, get extremely uncomfortable and forge through the above objectives. Nix began the program at ground zero as a white belt and noticed quickly that to “belong” he was going to have to put in everything he had physically and mentally to be a part of and build relationships with those in a different belt color. Nix shared, “I put forth the effort to belong. I learned their names. I had outgoing and positive energy. I acknowledged my classmates. I supported my team members. It’s as simple as saying ‘hi’.” As humans, being recognized is important to growth and being a part of a group gives value. All of those things build culture. Nix said, “Just say ‘hi!’ There’s power in belonging! Create a company culture that is team-focused. Build connections with employees and give recognition and appreciation when earned. ‘Blow the dust off!’”
Connect the Dots: How to Unleash Your Hidden Ingenuity!
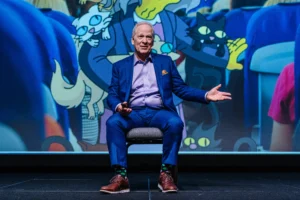
As he sat on an airplane with his headphones secured to his ears, ready for the plane door to shut, an older Russian lady walked through the door (Stainton thought, “What are the chances she’ll sit in the empty seat next to me?”), shuffled down the aisle, pointed at the empty seat and sat down. For the next five hours, he retreated, listening to music – his escape – until the plane descended to the final destination. That’s when the lady tapped him and said, “Is home for you?” The conversation carried on and she mentioned that she was from Russia and had not been back since she was a music teacher. ‘Connecting the dots,’ Stainton shared he was listening to the song ‘Firebird Suite’ by Stravinsky, and the lady said, “Ah. Stravinsky. The Firebird. I was with him when he wrote it.” Then the plane pulled to the gate and Stainton never saw her again. Separated by five inches and a pair of headphones, he shared with attendees that this experience taught him that people are different, but in those differences are amazing ideas, conversation and experiences. He said, “Your next breakthrough could be one connection away.”
Is there a master key? It turns out there is. It’s called innovation. The first shift is a mindset. Stainton said, “It’s believing that you are creative. So much of our existence is about what we choose to think about ourselves. It’s believing that you deserve to be there and belong; it’s not a private club but an open playground.” He continued, sharing that the innovator/breakthrough thinker asks the question “How can this be better?” Innovation comes in small, medium and large wins. Innovation is not about a lightning bolt moment but “connecting the dots.” People need to start being dot collectors and dot connectors, because when dots are connected, and connections are made, ingenuity happens.
Stainton said, “What if the dots were different sizes, shapes and colors? What if they were the ideas, experiences, people and different beliefs in life? When the blinders are taken off, these dots open new possibilities and bring opportunities.” Everyone should ask, “What’s the yellow dot here?”
More information: www.talk.ac/billstainton (enter code: MAPP)
Basically Incredible
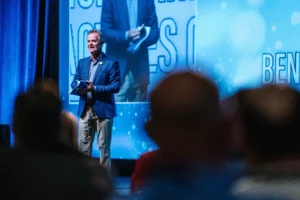
Delivering on what it takes to embrace a “basically incredible life,” Matt Booth engaged attendees by requesting each person to pair up and ask, “Tell me something good!” It wasn’t the typical question, “How are you?” It got attendees thinking and acting differently toward each other; in turn, shifting the energy and attitudes in the conference room. Following the exercise, Booth shared five basic principles to “Live an Incredible Life” including:
Attitude – It’s not always easy to have a positive attitude and it’s important to have strategies to pull employees in the right direction during tough times. Attitude is the start of everything, determining thoughts and then actions.
Communication – Within companies, it is extremely important to have the tools and techniques in place to communicate clearly and effectively.
Health and taking care of ourselves – Booth said, “There are no shortcuts.” Companies change direction for the better; people move in a positive direction because action is taken and something is done about it.
Have a plan/direction – It’s taking control of what can be controlled personally and professionally, including attitude, relationships, health, communication and so forth.
Have a source of power – To not only have the power to influence one’s mindset and attitude but to have the ability to influence another’s behavior, beliefs and actions.
“A small change in your attitude can make a big impact and create changes,” said Booth.
More information: www.mattbooth.com/basicallyincredible
Automation Hall Displays Latest Innovations
In its second year, the cutting-edge Automation Hall returned, bringing together the industry’s experts to display their cutting-edge technological advancements and automation achievements. Attendees explored the latest innovations and proven automation technologies that define excellence in top facilities across the US.
Staying Ahead of the Curve in 2025–2026
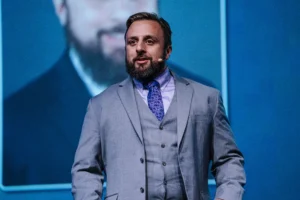
ITR Economics
A key member of ITR Economics’ team of expert economists and consultants, Michael Feuz contributes to the production of client reports, forecast reviews, economic research and regular client-facing communications. Taking a look at global markets and their impacts on US manufacturing, Feuz shared key insights into consumer spending, inflation, interest rates, the labor market and leading industry indicators. Lastly, he provided a high-level look at manufacturing’s outlook, including:
- Interest rates may ease lower later in 2024 and into 2025.
- The service sector is expected to hold up better than private manufacturing in 2024.
- Fiscal policy and high corporate cash levels and a buffer for the economy.
- Assess cash needs.
- Maximize competitive advantage.
- Think about expanding the asset classes invested in and plan to pivot hard in 2028-2032.
More information: www.itreconomics.com
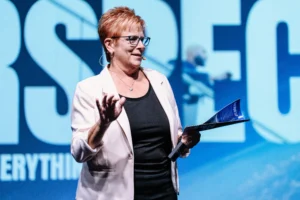
Wipfli
Presenting on Data-Driven Leadership: Empowering Success in the Plastics Industry, Laurie Harbour has more than 35 years of manufacturing and consulting experience. Providing insights from this year’s MAPP Plastics Benchmarking Study, she addressed market trends impacting processors, challenges and how to prepare for the good and bad through the end of the year into 2025. Harbour said, “Like previous years, the optimism felt by plastics processors at the start of the year has declined. This is due to many challenges, including flat revenue and increased costs for labor and materials.” As companies move through the year and plan for 2025, they must understand their businesses and using the MAPP Plastics Benchmarking Study can be helpful and guide preparations.
More information: www.wipfli.com/manufacturing
Manufacturing in the Era of Artificial Intelligence
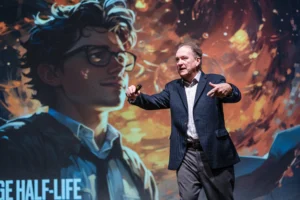
“Manufacturing is learning to work with the machines, and there will be future AI manufacturing careers,” said Carroll. He continued, asking attendees, “When it comes to a company’s ability to innovate, are you going to chase it or are you going to allow the future to happen?”
It’s time to stop avoiding innovation and get out in front of the progression in manufacturing. “Companies have to invest in experiential capital. Build an ‘Xbox room’ and explore the unknown with the next generation. Stop wasting time on frivolous things,” Carroll said. “Assess employee skill sets – become your future.” Carroll highlights the following:
- “The future belongs to those who are fast.” In thinking about the plastics industry and a rapidly changing world, what does it look like in 10 years? Companies need to adapt, reinvent and keep up with the speed of change.
- “Velocity is the new normal.” It is important to ignore uncertainty. Carroll said, “Is your company waiting 10-15 years for a recession that has yet to arrive – and it still is not here – when companies should be doing things that allow them to chase their future faster?” It’s a mindset.
- “Why now – not when?” Companies that adjust expectations balance the risk and reward because every trend goes through a curve of peak inflation, slope of enlightenment and plateau of productivity.
- “Why now – and when? It is key to understanding the opportunity. AI is not one thing; it is many things. The different aspects of AI are at different places on the curve.
- The future is coming at you faster than you think. For companies, challenging the methodology is part of the process and can lead to efficiency gains. “This is not Grandad’s farm anymore!” With the next generation of manufacturing within grasp, companies should absorb and implement generational changes.
“Above all – think big, start small and scale fast!” said Carroll.
More information: www.jimcarroll.com
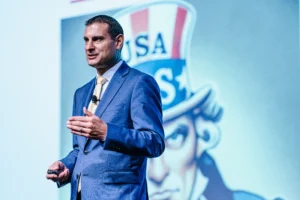
Inside Beltway
As a founding partner of Inside Beltway and having worked in the nation’s capital for over 25 years, Omar Nashashibi provided conference attendees with insights and updates from Washington, D.C., including the latest from policymakers, trade talks with allies, efforts to increase taxes and regulations, and what steps lawmakers can take to address workforce and supply chain challenges. In addition, he spoke about the November election and what the coming year could mean for the manufacturing industry.
More information: www.insidebeltway.com