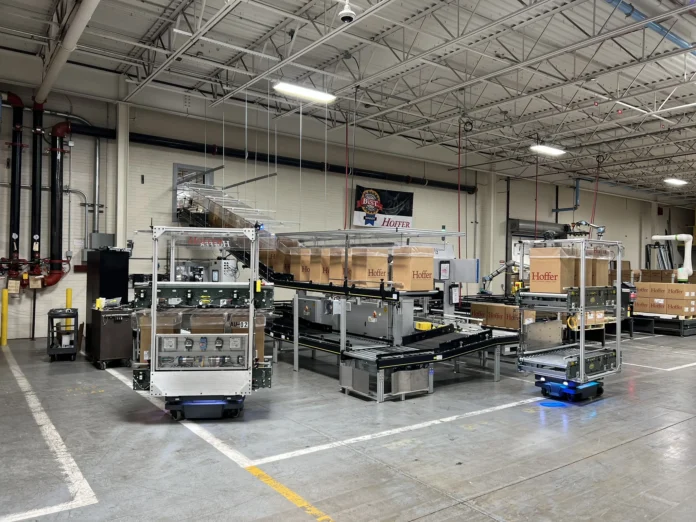
By Liz Stevens, writer, Plastics Business
Two MAPP member companies recently have implemented new production floor innovations, employing automated manufacturing elements that work seamlessly together as important pieces of today’s smart manufacturing puzzle. Flambeau, Inc. and Hoffer Plastics each zeroed in on production lines at their plants with the aim of reducing manual labor and streamlining processes.
Flambeau Tackles Product and Process Improvements with DFM, EOAT and More
Flambeau, Inc., headquartered in Baraboo, Wisconsin, and with operations across the US and in Mexico, UK and China, is a custom manufacturer of injection-molded and blow-molded parts, components and assemblies. The company serves numerous industries, ranging from agriculture and defense to recreational and transportation.
Flambeau recently re-engineered a 50-year-old trunk-style cantilevered tackle box for fishing aficionados to create the Flambeau-branded NextGen Tackle Box for contemporary recreational anglers. The company submitted a smart manufacturing submission covering this initiative to the 2024 MAPP Benchmarking and Best Practices Playbook.
The new product was designed with design for manufacturability (DFM) analysis and SolidWorks. The aim was to have most of the new product’s components produced in one cycle by a single mold. This minimizes the number of presses and operators required and eliminates handling and inventory of “in-process” parts.
The injection mold was designed to accommodate automated part handling and was fitted with cavity-pressure sensors to optimize the molding process for fast job start-up, maximum quality and minimized cost. Then, Flambeau automated the cooling, assembly and fastening of the product, eliminating operator error and ensuring accuracy and consistency. And, finally, InfraStake® staking technology was added as an integral component of the automation, delivering precision and control, rapid cycle time, reduced thermal stress, clean forming and low maintenance.
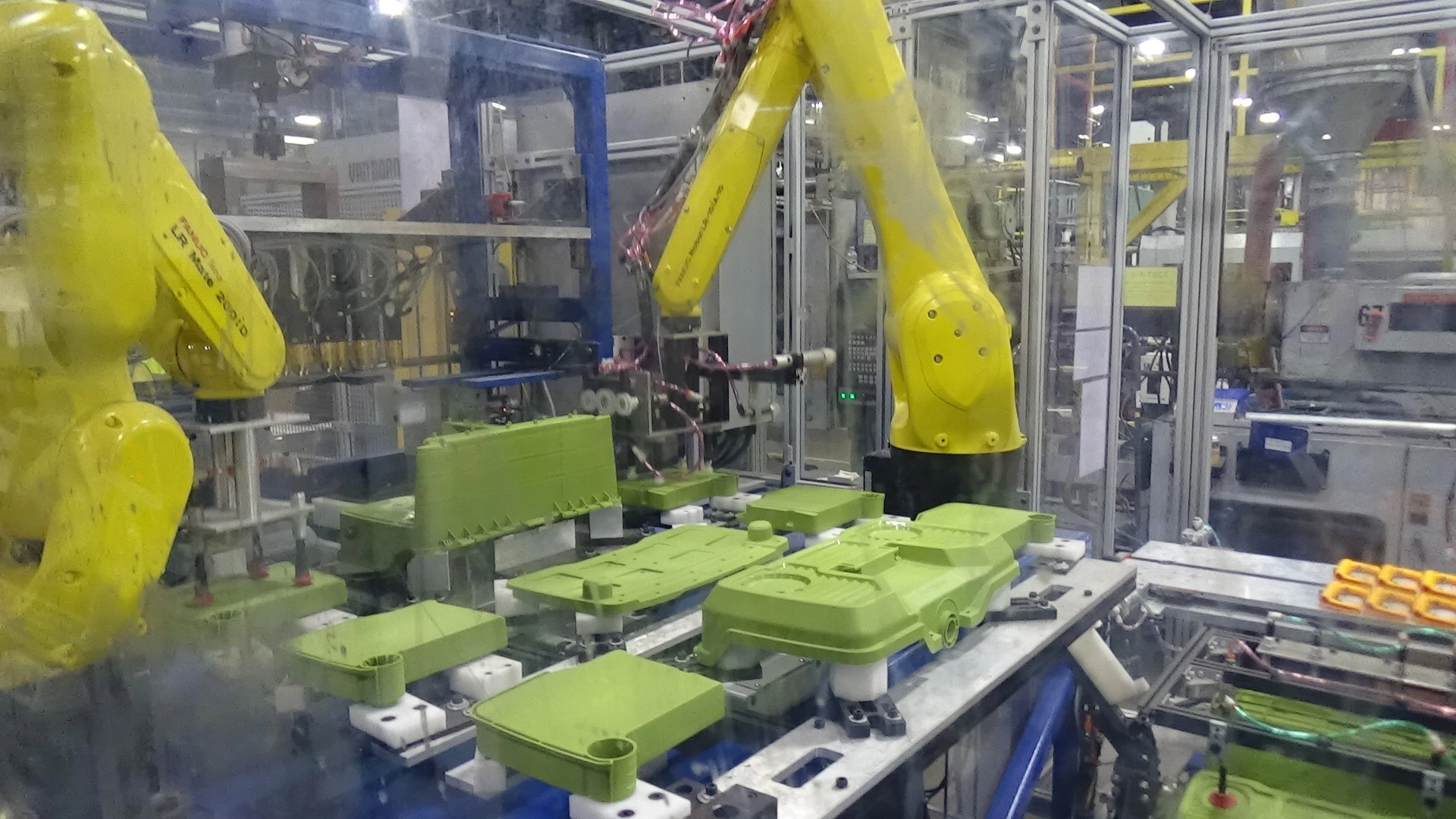
Automated part handling at the mold was implemented with Sepro Robot Strong 40 units. The robots lift and move seven components for the new medium tackle boxes or nine components for the large tackle box from the press to the assembly cell where two five-axis Fanuc robots move parts for assembly and, in one instance, hand parts off to one another. The final product is heat staked before the operator receives the nearly complete assembly to manually install a tag and a latch and complete the final product inspection.
The automation cell delivers a 95% finished product for a single operator to add the finishing components, inspect and package the item, and maintain a steady pace to meet the production demand. The impact on labor and production becomes evident when comparing the Hip Roof Tackle Box (an earlier model) to the NextGen Tackle Box. The Hip Roof model required three operators to produce 58 items per hour. The NextGen Tackle Box requires one and a half persons to produce 70 items an hour – a net gain of 12 items per hour with half the staffing. Overall, Flambeau’s automation delivered benefits in equipment usage, yield rates, labor, time to produce and packaging.
Plastics Business talked with Richard Zavracky, product development engineering manager at Flambeau, about these automation innovations. Zavracky manages new projects for the Flambeau retail line of products. He and his team create, design and test new innovative products.
Zavracky made strategic choices to design the new product’s injection mold and the product itself, with an eye toward automating parts handling and assembly. “There were a number of features and areas we had to be aware of before we could release our parts for tooling,” said Zavracky. “We had to make sure that each component had enough flat surfaces so that the end-of-arm-tool (EOAT), which was equipped with vacuum grippers, was able to pick the component up repeatedly. Parts were arranged in the mold so that the mold would fit inside a specific press size and allow for easy access by the EOAT and an easier transfer to the automation cell. With the parts already in an optimized location in the assembly cell, less time is required to manipulate them during assembly. We shifted the lid handle attachment location from the back side (traditionally) to the front side of the product, which creates a unique look and helped create a smoother assembly process.” Zavracky increased the wall draft in select areas to ensure that the parts would eject from the mold smoothly. “And for the mold design,” he said, “we included the required ejection bars and pins to help push the components off of the mold and onto the EOAT fixture.” One lesson learned in this area: “If one of the parts sticks in the mold and the EOAT is unable to grab it,” he said, “this creates a scrapped SKU and causes a cycle-time delay. It was important for us to ensure repeatable ejection of the parts.”
Another mold design decision was to add cavity-pressure sensors to maximize part quality and minimize operation costs. “A cavity-pressure sensor can help determine the quality of the molded part,” said Zavracky. “By measuring the mold-cavity pressure, we can determine if the cavity is filled with enough plastic to produce a high-quality part. Once we set a cavity-pressure profile, it helps us in the start-up process of the mold. A faster start-up process decreases the cost of the finished product since less time is spent optimizing the molding process before each production run to produce high-quality parts.”
Flambeau uses InfraStake®, a plastic heat staking technology to join components. “This process is used to join the main base of the tackle box to the sub-base,” Zavracky explained. “The main base has molded post features, and the sub-base has holes that align with these posts. During the heat staking process, these post features are heated, which softens them, and compressed down around the sub-base component to mate the two components together.”
Zavracky described the tackle box product redesign and the move to automated part handling. “Flambeau’s objective was to re-engineer the commonplace trunk-style cantilevered tackle box to create Flambeau’s NextGen™ Tackle Box,” he said. “Our goal was to deliver ‘newness’ for traditional trade retailers and to re-energize sell-through and brand relevance by increasing the value for a value-based product. We targeted fresh, improved utility and functionality, made in the USA with a modernized design.” Zavracky’s design for manufacturability analysis was aimed at reducing part count, minimizing fasteners, enabling automation and optimizing efficiencies for lean costs and maximizing profitability. “This product design,” he said, “required us to think ‘outside of the box’ and leverage advancements in manufacturing technology. This enabled us to produce a product that would not have otherwise been feasible.”
Zavracky said Flambeau measured success and progress of this innovation by comparing the final results to what was approved in the company’s capital expense report (CER). “Did we match our target manufacturing cycle time? If not, what steps can be taken to achieve this result? Did we match our target manufacturing cost? And did we achieve our sales volumes?”
Zavracky commented on the impact that automation, robotics and advanced, thoughtful redesign of molds can have on the industry as a whole. “These advancements already have made significant improvements in this industry,” he said. “The first few things that come to my mind are the consistency of quality parts that are being manufactured, as well as improved worker safety. These redesigns and robots can greatly minimize the risk of accidents and injuries that are associated with hazardous or repetitive tasks.”
Hoffer Employs AMRs, SCADA and More to Manage Production Tasks
Hoffer Plastics, South Elgin, Illinois, provides injection molding, tooling, engineering and value-added assembly for many markets, including food and beverage, lawn and garden, industrial, automotive and medical/pharma. The company submitted a smart manufacturing submission to the 2024 MAPP Benchmarking and Best Practices Playbook, detailing its initiative to use a supervisory control and data acquisition (SCADA) system to monitor and automate tasks and to dispatch autonomous mobile robots (AMRs).
Hoffer Plastics added several instances of automation. Its SCADA system works in concert with production lines that use specialized equipment in conjunction with custom box shuttles and MiR 250 AMRs to assemble, transport and fill empty cartons. Those cartons then are transported via AMRs to be closed, taped and palletized via a collaborative palletizer. The workflow is as follows.
When signaled by SCADA, an automated Pattyn box maker and bag inserter assembles a box and inserts a bag into it. The box maker ejects the new box, as instructed by SCADA, via a conveyor system either to a lining machine (the production line’s assembly cell), or up an elevator to an aerial staging conveyor for temporary storage. This provides a cache of empty boxes in waiting.
When the SCADA system wants more empty boxes dispatched to a production line, it alerts one of Hoffer’s AMRs, which have two-tier box-carrying structures mounted on them with motorized backward/forward conveyors. An AMR will go to a central conveyor location to pick up empty boxes. It will dock its conveyor to the box storage conveyor and – via communication with SCADA – will receive three empty boxes counted out by a sensor onto its conveyor, which are moved to the top tier of the AMR.
At the assembly cell, the assembly machine will assemble parts (in this case, bottle caps with lid liners inserted into them) and eject them via a conveyor. That conveyor will drop the parts into a box on the box shuttle, a two-tiered structure that is in contact with the SCADA system and also in sensor contact with the AMRs. The box shuttle has two-way conveyors, and it holds empty boxes for filling. In addition, the box shuttle controls the filling of its empty boxes with new products. Once a specified number of parts have been deposited, the box shuttle will send a signal to the assembly machine to pause, turn on its conveyor to move the full box out of the filling position and then move an empty box into the filling position. When three full boxes have accumulated on the box shuttle, the box shuttle sends a signal to the AMR that it is ready for pick-up.
The AMR goes to the box shuttle, offloads filled boxes from the shuttle’s lower tier to the AMR’s lower tier and delivers empty boxes from the AMR’s upper tier to the shuttle’s upper tier. After picking up filled boxes, the AMR goes to a Pattyn bag closer/case closer, docks to its conveyor and offloads filled boxes. The AMR disengages from the conveyor and then waits for a signal from SCADA for its next drop-off/pick-up job.
The case closer – controlled by SCADA – closes bags, closes and tapes the boxes, and sends boxes via conveyor to the collaborative palletizer. The SCADA system uses a Cognex barcode reader to read the barcode on the box label to ensure the product is appropriately sorted. Closed boxes then are sent via conveyor to a Universal Robot or a Fanuc collaborative palletizer, a six-axis robot that stacks boxes on a pallet to get them ready for shipment.
Adam VanMeter, automation project manager at Hoffer, provided insight into the complicated automation innovations in which he worked with Hoffer’s inside team and outside integrators to implement Industry 4.0 technologies. “We wanted to eliminate the repetitive tasks that our operators were doing,” said VanMeter. “Removing those repetitive tasks allowed us to focus on upskilling our team.” VanMeter and his group keep an eye on automation developments by attending tradeshows. “Seeing equipment out there performing the tasks that we perform,” said VanMeter, “made us realize that the technology is out there, and it is capable of fulfilling our needs.”
VanMeter and his team envisioned the innovations, gained approval and then began to execute their project plan. “We came up with a rough plan that allowed us to get quotes on the equipment we would need to purchase,” he said. “When we had an idea of cost, we put together a return on investment report to present to the executive team. Once they were on board, we refined our plan and began drafting the work area in CAD. We then began ordering equipment and installed it piece by piece once it arrived.”
With design, testing, implementing and finetuning any automation project with this kind of complexity, lessons will be learned. “Clear communication absolutely is critical,” said VanMeter. “Everyone must be kept on the same page on a project of this size.” In measuring the success of the project, VanMeter got that same kind of clear communication from the Hoffer workforce. “We did not put any hard metrics in place to measure success,” he said. “However, when I must take the system offline to do a software update or any kind of maintenance, the operators are upset that they have to go back to the old ways, even if it’s temporarily. To me, that is success. We have successfully made their lives easier and given them more purposeful work.”
Hoffer has more automation initiatives in the works. “We are working on a few artificial intelligence programs at the moment,” VanMeter said. “One AI hopefully is going to help our mold technicians create a more robust process on the floor. The other AI project that we are working with will help us inspect parts.” Hoffer benefits in at least two ways by innovating and making positive changes. “These changes will allow us to remain competitive within the industry,” said VanMeter. “They also show our team that we are committed to making their working life better and investing in their future.”
VanMeter sees initiatives like SCADA-controlled automation as offering important impacts for the industry. “SCADA could control nearly every aspect of logistics,” he said. “For example, a truck driver arriving to pick up a shipment could dock and use SCADA to scan their paperwork. From there, the SCADA system could know what needs to be put on the truck and dispatch an AMR to go pick it up and load it. Once successfully loaded, SCADA could print the outgoing shipment paperwork for the truck driver. “VanMeter views SCADA as a pivotal central element for automation. “The SCADA is the decision maker,” he said. “It tells everything else what is needed and where it is needed.”
AMR, DFM, EOAT and SCADA – these acronyms may spell out key elements for success in today’s and tomorrow’s advanced plastics manufacturing.
More information: www.flambeau.com, www.hofferplastics.com